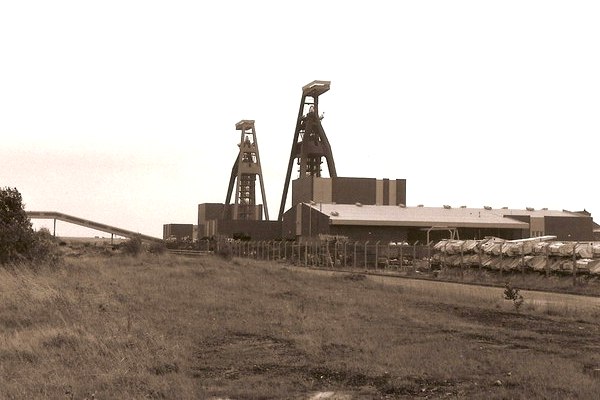
Thorne Colliery 1989
Copyright © Siobhan Brennan-Raymond and licensed for reuse under this Creative Commons Licence
On October 12th 1909 Pease & Partners Ltd, an iron making company with ironstone mines on the Cleveland Hills, began sinking shafts at Moorends, near Thorne. This was to become one of the longest and most difficult sinkings in the annals of mining. It was truly an ill-starred venture.
A local firm sank the two 6.7 metre diameter shafts to the Bunter Sandstone, where sinking was stopped for pumps to be installed and to allow the construction of head frames and winding engines. When sinking restarted the inflow of water increased rapidly and it was decided to use a German ground freezing system to overcome the problem. Sinking was delayed until December 1909 when the process began under German supervision. It is generally said that the outbreak of the First Word War stopped sinking, as the workmen went home, but the ‘List of Mines’ records no underground workers from 1912 to 1918 inclusive! This may be because contractors were employed, but men were still working on the surface.
When the war ended Pease & Partners Ltd chose to use the cementation process instead of freezing, and contracted with the Francois Cementation Co. Ltd to do the work. Sinking was resumed on March 18th 1919 and the shafts were completed in March 1926. The Barnsley seam was intersected at 845 metres, but it had lost the thickness enjoyed by many other Doncaster area collieries. Instead it was decided to concentrate on working the High Hazel seam at a depth of 788 metres.
Production from the High Hazel seam began in 1925 and the workforce grew rapidly. Coal was moved manually until 1933, when face conveyors were installed. Power loading, using Meco Moore cutter-loaders was introduced in 1952.
The incursion of water through the shaft linings became an increasing problem, however. Weepers were noticed in No.1 Shaft during 1936, and in 1944 water entered the shaft at a depth of 348 metres. Later that year cracks were found at a depth of 366 metres in No.2 Shaft. Patches were made, but on examination it was concluded that water was finding its way down abandoned freezing tubes and causing pressure which was beyond the shaft linings’ capacity to withstand.
The problem was so bad by 1956 that the NCB decided to close the colliery for an estimated two years in order to repair the damaged sections. One repairs were done, it was intended to install skip winding, drive loco roads and introduce mechanised mining methods. In 1958, when the project was well advanced, an underground connection made with Hatfield Colliery, but further cracks were found in No.2 Shaft’s lining. These took until 1966 and coincided with a contraction in the industry, so Thorne remained in mothballs. In 1970, a bulge which appeared in No.1 Shaft’s lining in 1967, worsened. It was repaired in 1973, but a second bulge appeared later that year. The cumulative effect of the repairs and patches was a significant reduction in the diameter of the shafts, hence their capacity.
In what was probably the last gasp of the “Plan for Coal” era, the surface was entirely cleared and futuristic steel headgears were built over the two original shafts. The old pit bottoms were refurbished and some preparatory work was done on sinking a third, coal winding, shaft 230 metres to the S.E. Adverse market conditions led to the scheme’s abandonment in 1986, however. Thorne was put on a care and maintenance basis, linked to Hatfield, but in 2004 Coal Power Ltd turned off the pumps, filled the shafts and demolished the headgear. Thorne had been fully productive for only 28 of its 95 years of existence!
Further reading:
- NMRS Records, Gazetteer of British Collieries
- Sections of Strata of the Yorkshire Coalfield, Midland Institute of Mining Engineers, 1927
- Hill, A. The South Yorkshire Coalfield: A History and Development (Stroud: Tempus, 2002)
- Hill, A. Colliery Ventilation (Matlock: Peak District Mines Historical Society Ltd, 2000)
- Hill, A. Coal: A Chronology for Britain (NMRS, British Mining No.94, 2012)