WHITWICK COLLIERY (SK 431146)
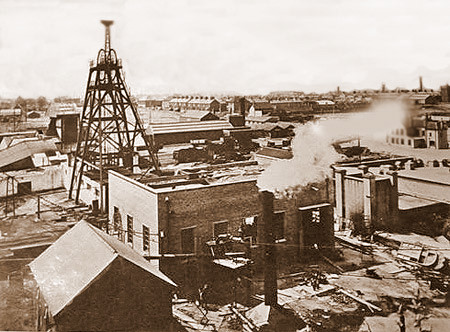
Copyright © www.healeyhero.co.uk and used under this Creative Commons Licence
Trial borings were carried out in 1822 near Long Lane (later Coalville) by William Stenson who was born in Whitwick. This was an attempt to prove that the coal seams in the exposed coalfield around Swannington, extended southwards under the cover of New Red Sandstones. Several workable coal seams were located and a small colliery opened in 1824. William Stenson, together with other financial backers, formed the Whitwick Colliery Company. Further areas with coal reserves were either purchased or leased and further shafts were sunk. The Main Coal Seam was intersected at 780 feet from the surface. An igneous intrusion was encountered in the sinking. This was in the form of a sill, approximately 57 feet thick. It became known as the Whitwick dolerite and has been mentioned previously in these notes in reference to the geology of the coalfield.
By the 1870’s, the colliery comprised five shafts, one of which was a pumping shaft and another, the upcast shaft. In 1876, a further shaft, No.6 or the “New Pit” was completed to 312 yards from the surface in order to win the Lower Main or Roaster coal seam. The Upper Main coal seam was intersected at 242 yards.
The Colliery Guardian magazine reported on Whitwick Colliery in October, 1896. At this time coal was being wound from Nos. 2 and 5 shafts and No.6 shaft – the “New Pit”.
Winding – The No.2 and No.5 shafts were 9 feet diameter with a single cage being wound in each shaft. One winding engine situated between the shafts served both shafts. The winding engine was made by John Swain of Hyde, near Manchester and was a twin cylinder horizontal, the cylinders being 24in. x 48in. and fitted with ordinary slide valves. Two reels for flat ropes were fitted on the crankshaft. One reel was 6 feet diameter bare for winding from the Upper Main Seam horizon and the other reel was 9 feet diameter bare for winding from the Lower Main Seam horizon. The cages were double deck carrying a single 12 cwt. capacity tub on each deck. The winding ropes were of crucible steel 4½in. wide by lino thick. Steel wire rope cage conductors were provided, three to each cage, and weighted 3 tons at the bottom. The headgears were of pitch pine, having two uprights 48ft. high and two backstays. Intermediate support pulleys for the winding ropes were provided between the engine house and the headgear pulleys.
At No.6 Pit, a twin cylinder horizontal winding engine was installed, winding two cages in the shaft which was 9 feet finished diameter. This engine was also built by John Swain of Hyde and had cylinders 36in. x 60in. fitted with Cornish Valves for steam admission and exhaust. The winding drum was of cast iron with three sets of 12 arms, each set having a brake path cast in. The drum was slightly conical, rising towards the centre, where the diameter was 17 feet. Overall width was 6 feet. Braking was by understraps acting on the brake paths and operated by foot pedal and levers.
The cages were double deck, carrying a single tub of 12cwt. capacity on each deck. Landings with two levels were provided at pit bank and pit bottom, allowing simultaneous loading and unloading of the two decks.
Winding ropes were of steel, 1½in. diameter, and each cage was guided by two rigid conductors of pitch pine 4½ inches square. Clearances in the shaft were tight. The headgear comprised two uprights, 16in. square at the bottom and tapering towards the top. Two back stays were provided. Height of the headgear was 60 feet and the rope pulleys were 10 feet diameter.
Underground Haulage – The haulage engine for the Upper Main seam of No.5 Pit was situated at the surface near to the upcast shaft. It was a twin cylinder horizontal engine, 16in. x 36in., built by Thornewill & Warham of Burton-on-Trent in 1894. The crankshaft was geared in the ratio 1 to 4 to a second motion shaft to which was fitted a 9ft. diameter Clifton pulley. An endless steel wire rope 1.125 in. diameter was passed for 2½ turns around this pulley and taken down the upcast shaft. A short distance inbye from the bottom of the upcast shaft a horizontal carrying a Clifton pulley was installed. The endless rope having passed down the pit was taken 3½ turns around the Clifton pulley, then half a turn around a tensioning pulley. From this pulley the endless rope returned up the upcast shaft and back to the haulage engine. Guide pulleys, 5ft. diameter were provided at the pit top and bottom.
On the horizontal shaft a second Clifton pulley was fitted, 6ft. in diameter around which the endless haulage rope was passed 4½ turns. This haulage rope served haulage roadways totalling more than 1¼ miles in length. Tubs carrying 12cwt. of coal were run in sets of twelve on the haulage systems, the sets being 260 yards apart.
Haulage requirements in the Lower Main seam were catered for by a haulage engine located near the top of No.2 Pit. This engine was a twin cylinder horizontal, cylinders 26in. x 48in., geared 1 to 2 to a second motion shaft to which was fitted a Clifton pulley 9ft. diameter. An endless rope was taken around the pulley 2½ turns and then down the No.2 Pit to a chamber 50 yards inbye. Located in the chamber was a horizontal shaft carrying 4 Clifton pulleys. The endless rope from the surface haulage engine was taken 3½ turns around the main pulley and after passing around a tension pulley, returned up the No.2 Pit to the haulage engine.
The other three Clifton pulleys were each fitted with a toothed clutch and each operated an endless rope haulage system. The first of these pulleys operated a haulage 2110 yards in length. The second pulley operated a haulage system 1650 yards in length. At 465 yards before its terminal landing, this haulage rope was taken 3½ turns around a 5ft. diameter Clifton pulley mounted on a vertical shaft. A second Clifton pulley on this shaft drove an endless rope which passed along a branch roadway to a 3-throw ram pump which was driven by this rope. The pump delivered water to the No.6 shaft sump.
Pumping – A beam pumping engine was located at the top of the pumping shaft and this engine was alleged to have been made by Messrs. Boulton & Watt at their Soho Works. The beam was of cast-iron and the fulcrum was mounted on the front wall of the engine house. From the nose of the beam a pitch pine pump rod 4½ins. square operated three lifts of 10in. diameter bucket pumps. The lifts were 47, 46 and 46 yards respectively.
The engine cylinder was 36in. bore by 8ft. stroke and had been renewed c.1895. The engine was equal beam giving a stroke of 8ft. in the pumps. Steam pressure was 6psi. and a vacuum of 11 inches was obtained. Normal working was 8 strokes per minute for 12 hours each day.
About 6 feet below the surface, a balance beam was located, attached at one end to the pump rods and weighted at the back end with 8 tons of metal. This assisted the engine on the upstroke of the pumps and steam under the piston in turn raised the balance box. From this it may be inferred that the steam cylinder was double acting.
Water was also raised at night at No.6 Pit by the winding engine and tanks under the cages. A small amount of water was also raised by the winding engine at No.2 Pit.
Ventilation – Ventilation was provided by a Guibal fan installed in 1890. The fan was 30ft. diameter by 10ft. wide, driven by a duplicate engine, one engine being in use at a time. Engine and fan ran at 44rpm., circulating 90,000 cubic feet of air per minute at 1.9 inches water gauge.
Boilers – Steam was provided at 50 pounds per square inch by three ranges of boilers, with a total number of 14, all hand fired. For Nos.2 and 5 Pits winding engine, three Lancashire boilers each 7ft. diameter by 30ft. long and three egg-ended boilers were provided. These boilers were roofed over. Boiler feed was by a live steam injector or alternatively by a steam driven pump. A square section chimney 80 feet high served the boilers.
Steam for the fan engine and the two haulage engines was supplied by three Lancashire boilers, 7ft.x 30ft., served by a square section chimney 60 feet high. Boiler feed was by an injector or a steam driven pump which had two 6in. diameter steam cylinders.
Five Lancashire boilers, 7ft. x 30ft. were installed at No.6 Pit and were served by a square section chimney 130 feet in height. Boiler feed water was drawn from a well sunk in the New Red Sandstones by a steam pump. The water was delivered through a pipe which passed through an old boiler into which the winding engine exhausted.
Underground Working – Both Upper and Lower Main Seams were worked on the longwall face system. The dip of the measures was 1 in 12 to the east.
Tubs were taken along the coal face to be filled and then hauled by ponies to the main engine haulage roads.
Open lights were used by the colliers but a safety lamp was kept burning at the lip of each working stall.
Coal preparation – A screening plant was erected at No.6 Pit c.1895 by The Butterley Company. This comprised a sorting and cleaning band, elevator and shaking screens. The sorting band was 150 feet long and 3ft. wide. Five graded sorts were picked off the band by hand. The elevator lifted the coal to three shaking screens. Dust was collected in a large hopper and loaded into railway wagons. “Peas” and “Nuts” fell into a hopper and then passed to a cleaning band 15ft. long by 2ft. wide. From this band the coal passed into railway wagons. Cobbles were cleaned in the same manner.
The plant was driven by steam engines. A 16in. single cylinder engine drove the main band and elevator and an 8in. engine drove the shaking screens and small cleaning bands.
Brickworks – A brickworks was sited adjacent to the colliery. Ten circular kilns produced a total of 100,000 bricks per week.
Fatal Accident – On 19 April 1898 there took place the most serious underground accident ever to occur in the Leicestershire coalfield. Just over a mile from the pit bottom, a serious fire broke out in No.5 Pit in the early hours of the morning. Roof timbers caught fire due to a gob fire caused by spontaneous combustion. It proved impossible to extinguish the burning timbers and the fire spread, trapping 40 miners of whom only five managed to escape. Over the next two days brick firewalls were constructed and the ventilation current reversed in order to starve the fire of air and to allow a recovery party to re-enter the pit. Of the 35 who lost their lives, the bodies of 12 were never recovered. The subsequent inquest revealed that there had been management complacency in taking precautions to prevent the outbreak of gob fires. The full report can be found here.
LATER DEVELOPMENTS – During the 20th century, the extensively worked Upper and Lower Main seams became exhausted and it was necessary to develop other seams at the colliery. By the mid-1940’s the Five Foot, Splent, Middle Lount, Nether Lount and Yard seams were being worked, the Yard seam being at the deepest horizon.
At the surface, the old 19th century boiler plant had been replaced by two John Thompson water-tube boilers fitted with mechanical stokers. Each boiler was capable of producing 20,000 pounds of steam per hour. Again in the mid-1940’s the boilers were worked alternately as one boiler was sufficient to provide all the steam required. Steam was required for the winding engines and the ventilation fan, although this would be a more modern replacement for the original Guibal fan.
Electrical power at 11,000 volts was purchased from the public electricity supply and no electricity was generated at the colliery.
Transportation and Winding – Early in 1945 schemes were put in hand to improve coal transportation both underground and on the surface. The general objective was to replace underground rope haulages by conveyor belts. Coal winding was to continue winding tubs put the use of tubs for transporting coal would be restricted to around the shaft bottom and between the shaft top and the screening plant at the surface. Tub handling was to be fully mechanised and automated. An underground roadway conveyor had already been introduced as early as the 1920’s, the equipment being manufactured by Messrs. Mavor & Coulson.
Two coal winding shafts served the colliery at this time. No.3 Pit wound the Five Feet and Splent seams. This shaft was 140 yards deep and 14 feet diameter which seems to infer that the shaft had been widened at some time previously. No.6 Pit wound the Middle Lount, Nether Lount and Yard seams. The shaft appears to have been widened slightly from 9ft. to 10ft. diameter at some previous time. Larger tubs of 30cwt. capacity, made by The Butterley Company, were introduced at No.6 Pit. These ran on 2ft. 6in. gauge tracks.
Under the new scheme, the upcast shaft was used exclusively for ventilation. No.2 shaft (presumably) was an emergency man-riding shaft and the pumping shaft supplied approximately 1 million gallons of water per week to Coalville Urban District Council. This shaft appears to have been re-lined down to 7 feet diameter. Materials and supplies for use underground were wound entirely at No.5 shaft.
To facilitate movement of supplies underground along the conveyor roadways, 18 inch gauge tracks were laid, the conveyors being uni-directional. These tracks were connected to No.5 Pit.
The trunk conveyors delivered to a central conveyor-to-tub loading station. In No.6 Pit the mechanised tub handling system at the loading station required the use of compressed air. As compressed air was not generally used at Whitwick Colliery, a small electrically driven Consolidated Pneumatic air compressor was installed locally to the loading station.
Underground Working – All seams were worked longwall, the wastes generally being strip packed except for one district in the Nether Lount where total caving of the waste was employed. Mostly the seams were worked on the advancing face system.
In No.6 Pit, the Yard Seam had a hard fireclay floor and a strong roof, and all the seam was extracted, the thickness varying from 2ft. 6in. to 3 feet. The Nether Lount which was about 30 feet above the Yard Seam was 4ft. to 5ft. in thickness. The strata was such that it was necessary to leave 9in. to 15in. of coal to form a roof. In the Middle Lount, which was about 5 feet thickness, it was also necessary to leave up approximately 9 inches of coal as a roof.
The distance between the Nether Lount and the Middle Lount seams Varied from 30 feet in the north of the colliery “take” to 3ft. 6in. in the south. In the No.6 shaft, the distance was 5 feet. Where the intervening distance was less than 9 feet, the Middle Lount face was worked “advance” to the boundary of the take. The Nether Lount was then worked back in “retreat” using the same gate roads previously driven for the Middle Lount.
At No.3 Pit, the Splent and Five Foot seams were about 20 feet apart, the Five Foot being above the Splent. Coal seam thicknesses were 3ft. 9in. to 4ft. for the Splent and 4ft. 9in. to 5ft. 3in. for the Five Foot. In both seams the nature of the strata meant that 6 inches to 9 inches of coal had to be left up to form the roof. The Splent had a soft fireclay floor and as water was frequently met with in all of the seams, the Splent floor was readily broken up.
Surface and Coal Preparation – A new pit bank or heapstead was built at No.6 Pit top, the bank being about 20 feet above ground level. A fully mechanised tub handling system was provided and the heap stead building was fully enclosed.
Tubs arriving from the pit were tipped on to a plate conveyor which conveyed the coal to the screening plant. Coal passing over a 2½ inch screen was further screened and hand cleaned on picking belts to provide Cubes, cobbles, hard nuts, deep hards, roaster hards and kitchen nuts. Smaller sized coal was transported by troughed belt conveyors through a flow regulating surge hopper to a dry cleaning plant. Three grades of coal were produced – cleaned slack, deep doubles, screened and baker’s nuts. Coal sized less than one eighth inch was supplied to the colliery boilers.
Further Developments – Further developments at the colliery in the National Coal Board era included the complete electrification of the surface plant. Coal faces were fully mechanised with cutter loader machines, armoured, scraper chain face conveyors and hydraulic roof supports. An underground connection was also made with Snibston Colliery and the colliery was merged with South Leicester Colliery in 1984.
Seams Worked (1952) | Five Foot, Middle and Nether Lount, Yard |
Manpower (1952) | 792 Underground, 207 Surface |
CLOSURE | 1986 |
Copyright © NMRS Records: Geoff Hayes Collection
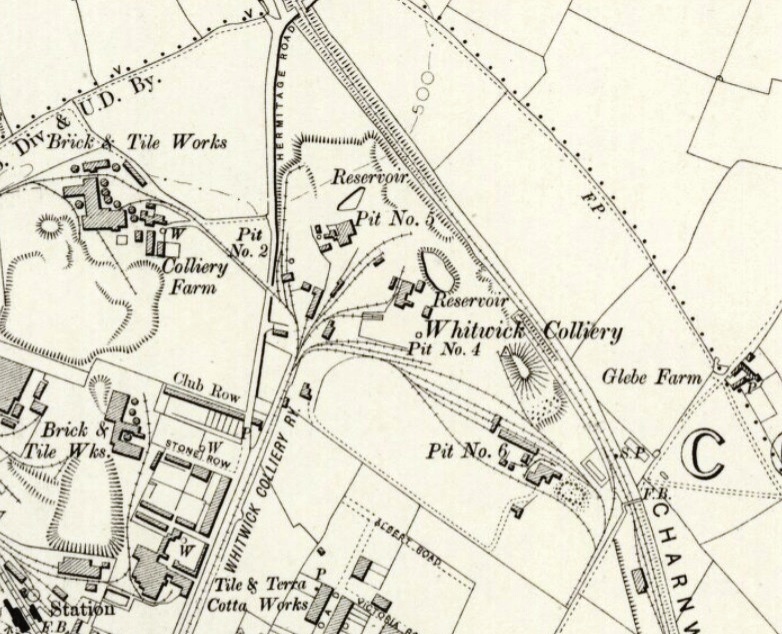
OS Map, Leicestershire XXIII.NE 1901
Reproduced by permission of the National Library of Scotland