BAGWORTH COLLIERY (SK 443086)
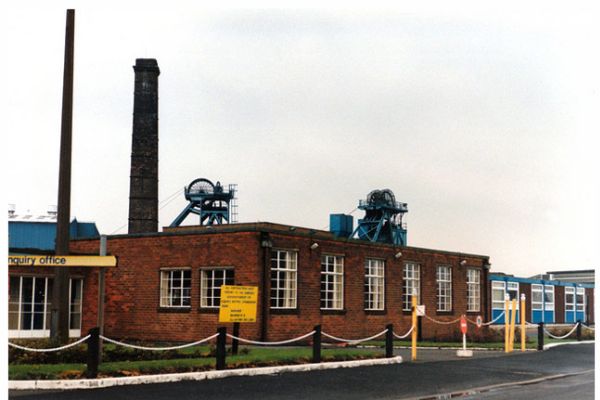
Bagworth Colliery
Copyright © Darren Haywood and licensed for reuse under this Creative Commons Licence
Sinking at Bagworth was instigated by the landowner Viscount Maynard in 1826. This was one of the early sinkings into the concealed part of the Coal Measures in Leicestershire. Thick coal seams were reached at quite shallow depth – the Stone Smut at 120 yards from the surface and the Swannington Five Foot at 124 yards. The seams were 9 feet and 6ft. 4in. in thickness respectively.
The colliery was ideally placed for the transport of its coal. Under the Leicester & Swannington Railway Act of 1830, the railway company had powers to construct a branch line to Bagworth Colliery. These powers were then transferred to Viscount Maynard, owner of the colliery, who built the branch line at his own expense. It came into use on 11 July 1832, the same day as the opening of this section of the Leicester & Swannington Railway. Connection was made into the main line of the railway by means of a turntable. When the railway diversion was built in 1848, avoiding the Bagworth incline, a conventional junction was made by the colliery branch line into the diverted railway.
Viscount Maynard died in 1866 and Bagworth Colliery was purchased by the Bagworth Coal Company Ltd. Labour disputes ensued from 1876 and the miners were locked out by the management. As a result of this the colliery was closed for a considerable period. Eventually the colliery company over-ruled the managing director and granted concessions to the miners so that the colliery could be re-started.
Reserves of coal were however becoming exhausted but the company managed to lease new reserves of coal from a Lady Brook in 1885. With this improved outlook, two new shafts were sunk to the Lower Main Seam. The seam was reached at 308 yards from the surface and was 8 feet in thickness. From this time the colliery appears to have been moderately successful but it was from 1947 and onwards that the greatest achievements were obtained.
Winding – Steam winding engines were in use at the two 1885 shafts until 1973. From the design of the two engines which survived until that time it seems very likely that they dated from 1885.
No.1 Shaft was the upcast ventilation shaft for the colliery. The winding engine was a twin cylinder horizontal with cylinders 22in. x 42in. Steam distribution was by ordinary slide valves. The winding drum was parallel with a brake path on each side and was a steel replacement of the original drum. The brakes were Markham calliper type. Stephenson’s link motion operated the slide valves and reversing was by a Melling’s (Worsley Mesnes) reversing engine. Overwind/overspeed protection was by a Melling’s pneumatic controller. Structurally the engine was typically nineteenth century with flat cast-iron bedplates and four-bar crosshead guides. The engine had been very hard worked in its lifetime but the bedplates seem to have survived intact and were without any visible repairs. Exhaust steam from the engine went direct to atmosphere.
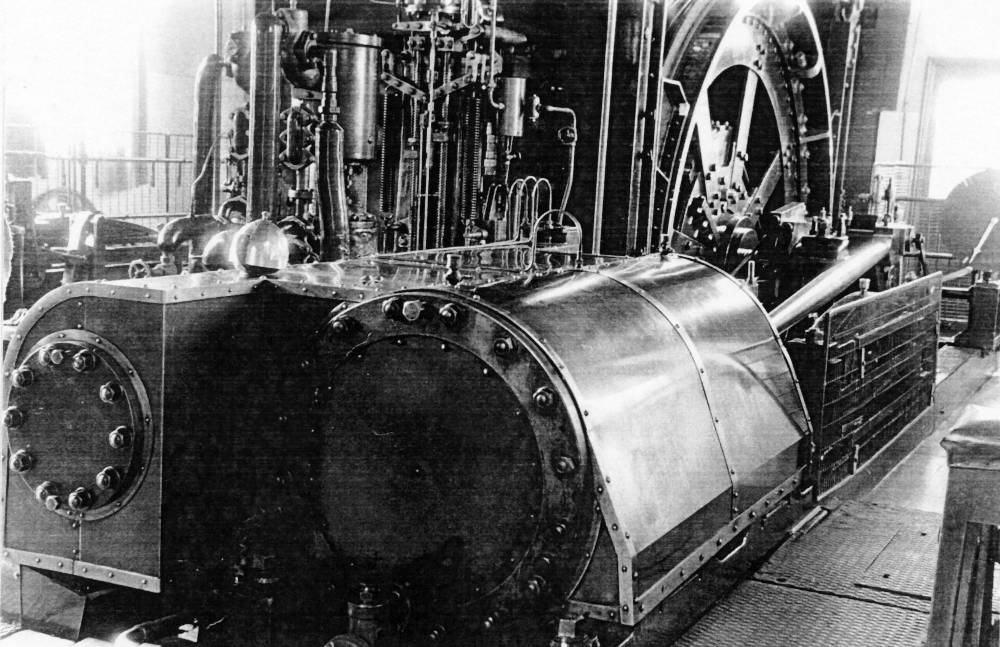
Twin cylinder horizontal winding engine at No.2 (downcast) shaft, as rebuilt with piston valve cylinders. G. Hayes 1972
No.2 Shaft, the downcast, had a winding engine larger than the No.1 Pit engine. It had been rebuilt with piston valve cylinders by the Worsley Mesnes Ironworks, Wigan, c.1953. These were plain piston valves without any cut-off control and were operated by Stephenson’s link motion. In spite of the modern cylinders the engine retained a nineteenth century appearance and seemed to be quite lightly built. The bedplate was of flat-bed construction and four-bar crosshead guides were fitted. A full range of Melling’s (Worsley Mesnes) auxiliaries was provided – pneumatic overwind/overspeed controller, reversing engine and brake: engine. The brake engine operated straight-post brakes which acted upon brake paths on each side of the winding drum.
Ventilation – Latterly an electrically driven fan provided ventilation but a steam driven fan was retained as a stand-by. A single cylinder inverted vertical engine drove the standby fan which was of the Sirocco forward bladed type. The engine was made by Marshall & Sons, Gainsborough, No.29525. The cylinder had a simple slide valve for steam distribution. The engine flywheel was 7ft. diameter but was not used to drive the fan. Drive to the fan was by multiple V-belts, the pulleys being sized to give a 1 to 1 speed ratio.
Pumping – Pumping was from a separate pumping shaft at which originally a non-rotative beam pumping engine was installed. The date and maker of the pumping engine were unknown. It appears to have been retained as a stand-by until Nationalisation of the colliery in 1947.
The cylinder was 63in. bore by 8ft. stroke and the cast-iron beam was 26 feet long. According to the late G. Watkins, the valve gear had been altered from 3-arbor to 2-arbor. With 3-arbor valve gear expansive working would have been possible but with the 2-arbor configuration steam would have been taken for almost the full stroke of the piston.
Three lifts of pumps were installed in the pumping shaft and each was operated by a separate wrought iron pump rod from the engine beam.
Old photographs show that the shear legs used for lifting the pumps and rods out of the shaft for repair were of timber. Photographs taken in the 1930’s by G. Watkins show that the timber shears had been replaced by an RSJ structure.
Compressed Air – Compressed air was employed for operating the cage decking gear at the shafts. Normally the air was provided by an electrically driven compressor but a steam driven compressor set was maintained in reserve. This set was made by Messrs. Reader of Nottingham and was powered by a single cylinder inverted vertical high speed enclosed engine.
Boilers – Six new Lancashire boilers made by Davy Bros. of Sheffield were installed in 1922. Originally these were hand fired and fitted with Meldrum’s forced draught furnaces. There was also an induced draught fan at the base of the chimney. The chimney was a square section brick structure. Working pressure of the new boilers was 100 psi and no economisers or superheaters were fitted. Neither was there a proper boiler house, the boiler tops, in the open air, being protected by brickwork. A shelter was provided over the firing floor.
By 1972 only four boilers were in service and these had been fitted with Danks’ chain grate mechanical stokers. The induced draught fan had been taken out of service reliance being placed on the integral forced draught fans of the mechanical stokers.
For boiler feed, 3 Lee-Howl direct acting vertical Simplex steam pumps were provided. This ensured that one at least of the pumps was always in reserve.
Underground Working – Coal was worked on the longwall system and under National Coal Board management cutter-loader machines were introduced. Latterly ranging drum shearer machines were in use which took out the whole seam.
Output per manshift eventually soared to more than 5 tons per manshift in the 1970’s maintained for a whole year. This was a count
ry-wide record. Apart from the efforts of the miners themselves this output was made possible by the use of cutter-loader machines on the coal faces, thick coal seams and the use of trunk belt conveyors to transport coal to the surface. The practice of packing the wastes from where the coal had been extracted was also abolished, total caving of the wastes was adopted together with the working of the coal faces in retreat. This reduced manpower requirements and speeded coal getting but in the relatively shallow seam depth surface subsidence was extensive and highly destructive to property.
Coal winding ceased at Bagworth Colliery itself and a drift was driven to connect with the surface at Nailstone Colliery. The shafts remained at Bagworth for winding materials, ventilation and access.
Seams Worked (1952) | Middle Lount, Yard |
Manpower (1952) | 719 Underground, 203 Surface |
CLOSURE | April 1991 |
Copyright © NMRS Records: Geoff Hayes Collection
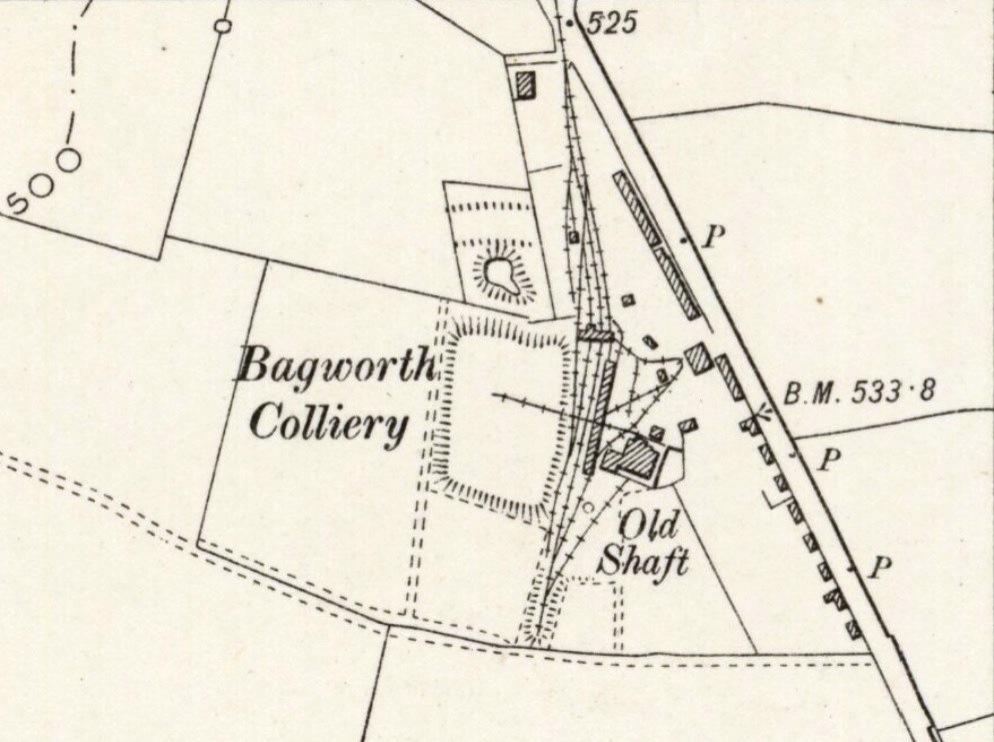
OS Map, Leicestershire XXIX.NE 1901
Reproduced by permission of the National Library of Scotland