At a site alongside the L&NWR Liverpool to Manchester line, Shaft Nos.1 and 2 were both sunk to find the Higher Florida seam, at a depth of 555 metres, during 1875 and 1876. No.1 Shaft, the upcast, is 3.66 metres in diameter, while No.2, the downcast, is five metres in diameter. The former company sank No.1 Shaft to its full depth, and No.2 to 183 metres when, in 1875, the pumping machinery was overpowered and the sinking was abandoned after £57,000 had been spent. The source of the water was the New Red Sandstone.
The Collins Green Colliery Co. Ltd was floated in 1875 and bought the plant at the Bold Colliery in 1878. Since then No.2 Shaft has been sunk to its full depth. A third shaft (No.3 Pit) was sunk to a depth of 564 metres between 1887 and 1890. It was 4.9 metres in diameter and passed through the Upper and Lower Florida seams. Its eventual full depth, according to cap, was 830 metres.
We are fortunate in that a detailed report on the colliery from December 1892 has survived. The following section is base on it.
The Collins Green Co. recovered the two shafts by using the winding engines to lift large barrels of water to drain them. The No.1 Shaft winding engine had two horizontal cylinders, 16 inches by 36 inches, which lifted barrels holding 300 gallons of water.
The No.2 Shaft winding engine had two horizontal cylinders, 36 inches by 72 inches, with ordinary slide valves. A cylindrical rope drum, 18 feet in diameter, with a brake ring at each side and a foot brake, also 10 inches steam reversing gear. It was used to wind water, and then for sinking to 183 metres. From which depth two decked cages, holding six tubs, were hauled. Each cage had three wire rope guides. The winding ropes were made of plough steel, 1.5 inches in diameter, which when half coiled on the drum were turned back by a ring so as to coil one upon another for half of the wind. This was found to greatly reduce the side abrasion which occurred when the whole of the rope was wound on the drum in one continuous coil sideways. The life of the rope was thus doubled. Each wind, including changing the tubs, took one minute, and 800 tons were raised daily in this shaft.
The No.3 Shaft winding engine had two horizontal cylinders, 36 inches by 72 inches, with ordinary slide valves. A cylindrical drum, 22 feet in diameter, with a brake ring on each side of the drum and a foot brake, also a 10 inches steam reverser. The winding ropes were turned back on the drum, as at No.2 shaft, and the cages and ropes were also similar. The colliery had no pumping engine, so water was lifted from the sump by the winding engine at night. Each winding rope was fitted with an Ormerod detaching hook.
The workable seams passed through in No.3 shaft at Bold colliery were:-
Workable coal (m) | Depth from surface (m) | |
---|---|---|
The Four Foot seam | 1.1 | 465.4 |
Yard Seam | 1.0 | 500.2 |
Higher Florida Seam | 1.0 | 548.6 |
Lower Florida seam | 1.4 | 553.2 |
All three shafts had 60 feet high pitch pine headgear in 1893.
On 20th January 1905 a serious accident happened as men were being wound down the shaft. For some reason the cage descended too fast, passed the mouth of the Yard Mine and crashed onto a sinking platform 30 yards below. 5 miners died and a further 14 were seriously injured. A full report can be found here.
The miners used Park Lane and Marsaut type safety lamps, with no open light being allowed away from the shaft.
The No.1 hauling engine was in the Upper Florida seam near the shaft. It had two horizontal cylinders, 16 inches and 30 inches, geared 1 to 5 and worked a 1 km long downbrow with endless rope of best plough steel, seven eighths in diameter. Originally, this engine hauled sets of about ten tubs up the brow to a distance of 640 metres the empty tubs descending by gravity. Under this system 700 tubs, containing 262 tons, were drawn per day. In 1888, however, the system was changed to an endless rope making it possible to draw 1,600 tubs, holding 600 tons of coal, in nine hours from a distance of one kilometre. The tubs were attached to the rope in couples at eight metre intervals. The old, 6 feet in diameter and 4.5 feet wide, engine drum was modified for use with the endless rope by fixing an iron plate, with a slight taper on the side, to one side of the drum. The rope was taken 2.5 turns round this plate, which was easily replaced when worn out.
No.2 hauling engine was placed near No.1 and had two horizontal cylinders, 16 inches by 36 inches, geared 1 to 3 and one 6 feet drum adapted for endless rope as above. The endless rope was taken 366 metres along the east level and a 275 metres long downbrow southward in the Upper Florida seam.
The main downbrow was driven one kilometre as an engine plane and extended over 100 metres to the face in the Upper Florida seam. The dip was 1 in 6.3 at the top and 1 in 7 at the bottom of the plane. Electric signalling was in use on all the downbrows. The coal was worked entirely by longwall. Levels are driven out of the brow 90 to 110 metres apart on the eastern side. The first level began at 155 metres from the top to allow a barrier of coal to be left at the Upper level and by 1893 had been driven 457 metres eastwards.
Six stalls were working at the far end of that level, and the coal tubs were hauled along it by horses to the downbrow where they were attached to the endless rope. The gateways in the stalls were about 15 metres apart and supported by packwalls and cut off every 90 metres by a new crossgate. The eight lower levels were driven out in the same way, but were progressively less advanced with depth, thus forming a continuous face with steps at 90 metre intervals. Because the coal’s cleavage (cleat) runs to the NE, the stalls were driving across it half on end, which was found to be produce more large coals. On the west side of the main downbrow the five levels were driven out about 180 metres apart. Jig-brows on half-course were used here. The coal from twelve stalls was brought by horses along each level to the endless rope. The face of work on the west side was continuous over 900 metres, being broken by steps at each level.
The Lower Florida was worked about three years after the Upper coal was got. It is about four metres below the Upper Florida, and was won by driving short horizontal tunnels from the levels in the latter seam. It was then developed by levels on either side corresponding to those in the mine above. The gates in the Lower Florida mine were 18 metres apart with packwalls 3.2 metres thick on each side, leaving about nine metres of waste in which pillars, three metres square, were built two yards back from the face as required. Two lines of props support the roof at the face.
In working the Florida seams the coal stuck to the roof requiring blasting to bring it down. The explosives Carbonite and Roberite, initiated by battery fired detonators on 36 metres of cable, were used for this. All were under the charge of shotlighters and the shots were fired day and night.
On the surface there were five Lancashire boilers, working at 70 lbs pressure. Three, by Messrs Hough and Son of Wigan, were 20 feet by 7 feet and two, by Tetlow Brothers of Hollingwood, 30 feet by 7.5 feet. There were also three steel boilers, by Messrs Heaton of Holt Town, Manchester, 30 feet by 8 feet, giving 100 lbs pressure. Another three vertical boilers 6.5 feet high and 4.5 feet in diameter with sixty Field tubes fitted to each boiler were house underground. Their feed water came by 4 inch pipes, giving a water column of 90 yards, from a cistern in the shaft.
At No.2 shaft at Bold colliery there are three ordinary bar screens. From one of the screens a travelling steel band, 45 feet long and 4 feet wide, was used for cleaning the large coal. It was driven by engine with one cylinder, 6 inches by 12 inches, and geared 1 to 4.
Bold colliery ceased to be profitable in the late 1930s and the Sutton Heath & Lea Green Collieries Ltd took over from Collins Green Colliery Co. Ltd in 1940. In 1942/3 it deepened Nos.1 and 2 Shafts to the Rushy Park Seam at 839 metres. It also introduced 15 cwt capacity tubs, built a new screening plant and renovated some of the surface buildings. The cages were double-decked, with each deck holding two 15 cwt tubs. The headgears by then were of steel construction.
When the National Coal Board took over in January 1947 Bold had two steam driven winding engines, built by Worsley Menses in 1903, on Nos.1 and 2 Shafts. These, the steam compressors, fan and boiler plant, were, with few exceptions very old and unsuitable given the colliery’s expected life and proposed output levels.
The Bold area had favourable geology, and three deep boreholes, sunk to the south of the colliery, confirmed that it extended a considerable distance. This gave Bold an estimated 61,000,000 tons of workable reserves. On this basis, the Central Electricity Authority decided to build a new power station next to the colliery. The NCB, therefore, began a major reorganisation in November 1949 and completed it in April 1955. The intention was to achieve a four-fold increase in output by 1961. Details of that scheme, written in June 1962 follow.
The pit bottoms at Nos.1 and 2 Shafts were mechanised and that at No.3 was modernised to cope with the increased output.
At No.1 Shaft an electric-powered Koepe wheel type of winding engine, with a driving pulley 26 feet in diameter, had been installed. The pulley was driven through single-reduction helical gears by two D.C. motors with R.M.S. rating of 1,800 h.p. The steel head frame had been replaced by a tall, reinforced concrete headgear and three deck cages had been installed. The latter held two, one-and- half ton mine cars per deck. It was planned to increase this nine ton load to 12 tons by installing four deck cages around 1970. This would increase the shaft capacity to 350 tons per hour. The pit top and pit bottom car circuits were mechanised using rams, tilting platforms and other tub control equipment.
No.2, downcast, Shaft wound coal from the 550 metre level. The pneumatic tub handling equipment at the top and bottom of the shaft had been modernised. A new reinforced concrete headgear had been built and the two deck cages were replaced by two three-deck cages. A balance rope had been fitted.
The steam winding engine was replaced by a Messrs Metropolitan Vickers electric winder. It had a single cylindrical drum, with a diameter of 15 feet, and was driven, through single reduction double helical gears, by a single 1,200 H.P. synchronous slip ring induction motor at 407 r.p.m. The shaft capacity was 165 tons per hour.
No.3 Shaft was deepened from the Wigan Mines horizon to the Rushy Park level in 1945. It is 16 feet in diameter and was used for downcast ventilation and emergency manriding. The original wooden headframe was replaced by a temporary steel headgear in January 1961. The Wilkinson’s steam winding engine was very old so it was replaced by an electric winder, identical to the one used at the No.2 shaft. In the reorganisation this shaft was used for supplies and manriding, but it became upcast. A new reinforced-concrete headgear, with the necessary airlock, was built.
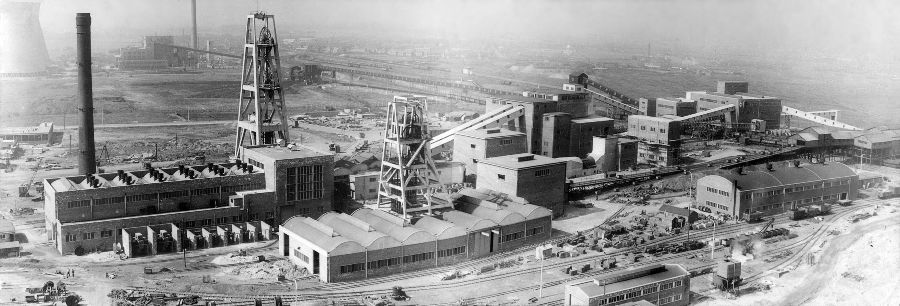
Bold Colliery, Newton-le-Willows, 1955 – From the Cliff Payne Collection
The old system whereby full tubs gravitated from No.2 shaft to an endless chain haulage which hauled them to the screening plant, where they were tippled and returned to the shaft, was no longer suitable. The new arrangements at the surface of No.1 Shaft included pneumatically operated car control equipment which propelled the full cars from the cages. After weighing, the cars travelled foreword through a shunt-back and gravitated to the tipplers. After emptying, the cars were elevated by a creeper and returned, through a shunt-back, to the cages for re-loading.
A new self-contained tub circuit was built at the top of No.2 Shaft and pneumatically operated tub control and cage loading equipment was installed. The original 15 cwts capacity tubs were retained.
As well as for man riding and supplies, No.3 Shaft was now used as an upcast from the 550 and 837 metre horizons. Pneumatically operated car handling equipment was installed at both the surface and underground, along with the necessary airlocks incorporated in the headgear structure.
The tipplers at Nos.1 and 2 Shaft delivered the coal or dirt onto two parallel plate feeders, which controlled the flow onto two conveyors leading into the screening plant. Coal from other collieries could also be handled.
The original screening plant’s capacity was 800 tons per shift. There was no washery and all qualities were dry cleaned. The run-of-mine was wound in tubs and after tippling was taken by two conveyors to two classifying screens. Over eight inch material was screened and passed to a circular picking table where the dirt and pickings were removed by hand, and the large coal was loaded into railway wagons.
The under eight inch went on inclined scrapers to three 400 ton capacity bunkers. These fed vibrating feeders at a controlled rate and delivered it to raw coal screens in the Coal Preparation Plant. The latter screens sized the eight inch to two inch for treatment in the dense medium system and two inch to zero for treatment in the two Baum Boxes. A proportion of half inch and zero was also extracted in these screens for mixing with washed smalls to give the required ash content.
The Dense Medium plant used froth flotation tailings as the medium to treat eight inch to two inch material in the deep bath. The clean coal passed over rising screens and on to classifying screens. The bath was operating at a clean coal gravity of 1.4s.g., and the sinks at this gravity were then separated by an upward current to give middlings and dirt. The middlings were rinsed and then crushed and passed on to the Baum Box feed. The dirt, after rinsing, passed to the main dirt disposal belt.
The two inch to zero was passed to two Baum boxes, after a proportion of the less than half inch was extracted. The clean coal went to classifying and dewatering screens. They were fitted with a top deck of half inch round meshes and a lower deck of 0.5mm wedge wire. The greater than half inch material joined the clean coal from the Heavy Medium System and passed to the final classifying screens. The half inch and 0.5mm was taken to one of the two centrifuges. The water and the fine solids passing through the 0.5mm wedge wire sieves gravitated to settling sumps where solids which settled to the base were pumped to the froth flotation plant. The clean water overflowing the sumps was reused in the washing boxes.
The thickened solids from the sumps were delivered onto two of three Niagara screens fitted with stainless steel woven wire cloths. The underflow from the Niagara screens gravitated to conditioner tanks where the froth agent was added and the pulp was then passed to the froth flotation cells. The clean froth passed to rotary vacuum filters and then recovered cake mixed with washed smalls.
The tailings from the froth flotation cells passed to a thickener; on the way a suitable flocculent was added. The clarified water was reused and the thickened tailings were mainly pumped to the dirt heap. As mentioned earlier, some part of the tailings were used in the Dense Medium System. The washed smalls were normally taken on a belt conveyor to the adjoining power station, but they could also be diverted to railway wagons.
A Landsale Office, Weigh Office and eight 50-ton capacity bunkers were built. In the late 1960s it was handling up to 5,500 tons per week.
Under the previous method of dirt disposal, both from screens and the pit, dumpers took waste onto a disposal ground near the colliery. The modernisation scheme incorporated facilities for preparing dirt for pneumatic stowing underground when required, but when this description was written, dirt was being conveyed to a loading point on the spoil heap, from where it is taken by a 30 ton capacity dump truck and tipped onto moss land.
The original surface buildings were old and unsuitable for inclusion in the scheme and so were replaced by new structures. The boiler plant was not required and was replaced by small boilers for space heating and pithead baths only.
The original air compressors were a modern Daniel Adamson steam turbo with a capacity of 6,500 cubic feet of free air per minutes at 80lbs per square inch, and a Walker reciprocating horizontal compressor with a 3,500 c.f.m. capacity. They were replace by three Bellis & Morcom two stage reciprocating compressors, each with a capacity of 5,230 cubic feet per minute, at a pressure of 80lbs per square inch, along with one two stage compressor of 2,700 cubic feet capacity for light duty load.
Before the reorganisation the 6.6KV electricity supply came from St Helens Corporation. It was transformed down to 550 volts and all equipment both surface and underground, was operated at this voltage. The maximum demand was about 850 KVA and a new substation was built to house the various switch-gear. Transformers are of the out-door type. After reorganisation the supply was purchased from the Merseyside and North Wales Electricity Board at 6.6KV and transformed down to 3.3KV and 550 volt. It is expected that the maximum demand will be 8,000KVA say 0.9 lagging power factor.
The old ventilation came from a 150h.p. electrically driven Walker Indestructible Fan at the top of the No.1 (upcast) Shaft. Its rated capacity was 400,000 cubic feet per minute at five inches W.G. when running at 110 r.p.m. The fan was running at 679 r.p.m. and circulating 175,000 cubic feet at 2.5 inches water gauge and so was not suitable for the colliery’s future requirements.
Two new fans were installed near the top of No.3 Shaft. One was a single inlet radial flow fan, of the back and aerofile type, manufactured by Aerex Limited. It was capable of a maximum of 600,000 c.f.m. at 16 inch water gauge and was driven by a 2,000 h.p. synchronous motor through a three speed gear box. It could not reverse the air flow. When the report was written this fan was moving 480,000 c.f.m. at 11.2 inch water gauge.
The other fan, manufactured by Davidson & Co. Ltd, was a three stage axial flow fan 12 feet 6 inches in diameter. It was could supply up to 540,000 c.f.m at 11 inch water gauge and was driven by two 750 h.p. motors. This fan was used as a standby and for reversing the ventilation.
The scheme for reorganisation underground was concerned with the development of the 837 metre horizon at No.1 Shaft. Here, a new pit bottom tub circuit was laid out and equipped with up to date tub handling equipment, tilting platform, deck rams, etc. A locomotive garage, battery charging station, electricity sub-station and water lodgement were constructed within the circuit.
Two cross-measures drifts, for use as locomotive haulage routes, were driven to link the shafts with the main field to the south. They were lined with fifteen to sixteen foot steel arches 13 inches thick. The drifts had reached a distance of 1,740 metres from the shafts, having passed through the Trencherbone, Wigan Four Feet and Wigan Five Feet seams with branches to serve the east and west area of the Rushy Park seam. Faces in the latter and Wigan Four Feet seams began work in April 1955 and were producing around 2,200 tons per day at the end of 1956. The total output of the colliery is 4,100 tons per day.
The loco-drifts served as intake airways. The return airway from the East Rushy Park area was in the Rushy Park seam and for the main south development and West Rushy Park area the return was in the Wigan Five Feet and Wigan Four Feet seams. This return connects with the No.3 (upcast) Shaft, 183 metres above the 837 metre horizon.
At the time of writing, No.1 tunnel had been extended to connect with the Yard Seam, which was then worked from No.2 Shaft, in order to provide improved ventilation in the Yard and Crombouke seams.
Loading stations, designed to allow quick loading with a minimum of labour, were constructed on the main locomotive tunnels serving the East and West Rushy Park areas and the main area development of the Wigan Four Feet Seam. The coal was transported from the faces to the loading stations by a one metre steel plate conveyor and 35 inch belt conveyors. Transport to and from No.1 Shaft bottom was by battery locomotive hauling trains of 60 to 30 cwts capacity mine cars per journey.
All faces were fully mechanised and equipped with power loading machines and armoured flexible conveyors. Three faces were equipped with Dowty self-advancing powered supports. In 1955 power loading was introduced on three faces giving a face O.M.S. of 33.7 cwts. By the end of 1958 all the faces at the colliery were fully mechanised and at time of writing the face O.M.S. was 114.2 cwts with an overall O.M.S. of 41.4 cwts. Coal getting was on two shifts per day on all faces except one which was recently been put onto three shift operation.
It was proposed to stow the Trencherbone goaf pneumatically. The stowing dirt to be sent inbye in the 30 cwt capacity cars from the surface and emptied at a dirt tipping station in the No.1 Main South Tunnel. The empty cars would then pass on to the end of the coal loading stations.
In order to produce the saleable output of around 3,500 tons of coal per day, it was expected that the labour force would have to be built up to 2,000 men, The local housing situation was difficult and large numbers of men were imported by public and private transport from neighbouring town and villages. The position was relieved by the allocation of houses for the mining community by the Warrington Rural District Council. In addition, the Coal Industry Housing Association’s plan for the Derbyshire Hill site had been completed. Six hundred and twelve houses and a three storey block of fourteen flats had been built and tenanted.
Bold pioneered the use of ELSIE (Electronic Signalling and Indicating Equipment) in 1965. Using it, the men in a surface control room, could monitor the progress of coal face bunkering, transport and all other underground and surface operations. It also provided data on water pressure, air pressure, smoke, ventilation flow and methane within the workings. The system underwent modification in order to better reflect the needs of efficient management.
Other innovations included a monorail for transporting the men in 1962, and a ripping machine, which was successfully tried in the Crombouke seam in 1963-4.
After the 1954-56 reorganisation (described above), Bold was profitable, but in the late 1960s the output fell below the planned level owing to restricted face room because of the need to avoid seam interaction and a shortage of manpower.
Production from the Crombouke seam ended in 1970 and all the output then came from faces in the Wigan Four Feet and Trencherbone in the main area of the ‘take’ along the 837 metre (915 yards) level. It was planned to increase output from 738,000 tons in 1970-1 to 833,000 saleable tons per annum by 1974-5 at an overall O.M.S. of 46.5 cwt with 1604 men on books. In order to do this it was necessary to exploit reserves in the Wigan Four Feet in the south area and the Trencherbone on the east side of the horizon tunnels, as part of the normal development of the colliery. A total of 10 kms of tunnel drivage from present access roads and 795 metres of straight drivage in the Wigan Four Feet and Trencherbone seams were required to provide current continuity and future additional capacity to enable four faces and one spare to be maintained.
The output was conveyed to the 837 metre level by the 42 inch trunk conveyor system to a central loading point on No.2 Horizon tunnel, located 1.1 km from the pit bottom. Coal was loaded into 30 cwt capacity mine cars and transported by battery locomotives for winding at No.1 Shaft which was operated at full capacity dealing with 3,700 tons per day gross. At approximately two kilometres inbye on the horizon tunnel Nos.1 and 2 pit haulage systems were connected by a 1 in 3.5 rise tunnel which was equipped with a 36 inch conveyor system. The output in excess of the winding capacity of No.1 shaft was diverted up this tunnel onto the No.2 pit coal transport system for winding at that shaft.
The battery locomotives and mine cars were installed during the 1955 reconstruction of the colliery, and the cost of maintaining them was becoming excessive by 1971. Their renewal was necessary. The chosen option of using trunk conveying to No.1 Shaft and only using locomotives and mine cars for moving men and materials was more beneficial and offered a saving in manpower. The introduction of the skip winding at No.1 shaft was considered, but judged not to justify the expenditure involved.
The following faces were then in production:- W11, in the Wigan Four Feet, was 208 metres long, with a seam section of 1.6 metres which was totally extracted. It had a single ended ranging shearer and powered supports. Production was on a two shift per day basis and the planned level of output was 800 tons per day saleable until replaced by W.10’s after which it would be held as spare capacity until required for production in April, 1972.
W3, in the Wigan Four Feet, was 189 metres long with a seam section of 1.67 metres which was totally extracted. It had a single ended ranging shearer and powered supports. Production was on a two shift per day basis and the planned output was 780 tons per day saleable. The face will finish in March 1972 and will be replaced initially by T.10.
T.2, in the Trencherbone, was a new 183 metres long face. The section of coal extracted was 1.73 metres with about 0.23 metres of top coal left up to form the roof. The face was equipped with a double ended ranging drum shearer and powered supports. Production was on two shifts per day basis and the planned output is 880 tons per day saleable. The Trencherbone is 33 metres below the Wigan Four Feet and T.2 face is working in an area extensively proved in the Wigan Four Feet. The face is expected to continue in production until June 1972 when it will be replaced by T.4.
The southern limit of workings in 1971 was against a 52 metre downthrow fault which had been seen in the Crombouke, Yard, Higher Florida and Wigan Four Feet seams at different points. To ensure continuity of production after September, 1973 it was necessary to tunnel through the fault from existing roads in the Wigan Four Feet seam in order to establish face room on the south side.
Preparatory work was proceeding on repairs to the existing gate roads of the old W.1 face which formed part of the main access to the south area and a start had been made on tunnelling through the fault on the intake side. Around 524 metres of tunnelling and 485 metres of seam road drivage were needed to reach the position of a pilot face which was to be advanced southwards to prove the area. The layout provided for proving the area further by driving headings to the east and west in the seam using continuous miners. That would enable flank faces to be worked to the south in substantially proved ground. Bold would become increasingly reliant on the Wigan Four Feet in the South area during the 1970s.
W.6 face, in the Wigan Four Feet, had been stopped prematurely owing to adverse roof conditions 180 metres short of the Twenty Acre fault’s expected position. It was proposed to advance the main and return roadways of this district eastwards to prove the ground up to the Twenty Acre fault. The expected downthrow of the fault was 300 metres to the east and eventually a tunnel would be driven through it to prove the area up to the Downall Green Fault.
In order to provide capacity in No.1 Pit for four production faces and a spare face, it was proposed to work the reserves of Trencherbone on the east side of the horizon tunnels in an area where the Wigan Four Feet above had been totally extracted. It would be necessary to drive 410 metres of tunnel and 104 metres in the seam from existing intake and return roadways in W.3 Wigan Four Feet district. A 183 metre face (T.10) was to be developed to advance northwards for about 640 metres at which point the area would be further developed by driving two headings beyond T.10 to allow four flank faces (T.11, 12, 14 and 15) to be worked. The tunnelling work to gain access to this area of Trencherbone had begun as T.10 face had to be available by March 1972.
To work the Trencherbone on the east side it would be necessary, because of the effect of interaction, to replace the east side man return in the Wigan Four Feet by re-routing the return air up the J.57 connection tunnel and via the Yard seam brows to the upcast shaft. That would also enable a second intake airway to be established from the horizon tunnels inbye to Wigan Four Feet 8’s West Level. That would involve driving a 144 metre long connecting tunnel, rising at 1 in 3, from a point on W.3 return.
A full methane drainage system was operating in all districts and now that coaling had ended at No.2 Pit, the methane ranges have been interconnected with those in No.1 Pit and most of the gas was now exhausted to the surface through a 10 inch diameter range installed for this purpose. The purity of the methane was insufficient for utilisation.
During the five years from September 1971 the seams to be worked were: the Wigan Four Feet and the Trencherbone. These had been worked out to a large extent in the past few years and in the main area were not expected to give any serious problems of thickness, structure, quality or workability.
In the southern area, i.e. to the south of the Main area, only two boreholes had been drilled, the nearer a quarter of a mile south on the 170 feet fault was not deep enough to prove the Wigan Four Feet and deeper seams. In the other borehole, one mile further south,, identification of the lower seams is not positive, however, it seems probable that, in the worst circumstances, the Wigan Four Feet will be workable for some distance to the south of the Main Area. The development had been designed to explore the southern area in such a way as to expose faulting and any features which may impose a limitation of the continued workability of the Wigan Four Feet.
The Wigan Four Feet and Trencherbone seams in the main and southern areas were both around 1.5 metres in thickness and of moderate quality, through the Trencherbone had higher sulphur (2.5% against 1.5% in the Wigan Four Feet). The Wigan Four Feet will be marginal 502 rank in future workings, but in the main area and to the south the Trencherbone was likely to be 610 rank for the next five years working in the eastern part of the main area.
In the Southern area the main exploratory work was expected to be in the Wigan Four Feet, though this could be transferred to the Trencherbone followed by the Lower Florida (similar quality and thickness and quality but 602 rank) should the Wigan Four Feet seam deteriorate. Exploration to the east, up to and through the twenty Acre fault was also planned and this may allow an extension of the classified reserves in that direction.
Total classified reserves of 15.2 million tons in the southern area was conservative. Of the 15.2 million tons, 9.2 million tons in the main area and 6 million tons were expected to be recoverable from the southern area. To the east of the Twenty Acre Fault a further 2.5 million tons may be recoverable. No account was taken in the classified reserves of other seams such as the Higher Florida or Arley which might be worked. The reserves in these seams are at present unclassified. Total reserves are 8.2 million tons.
In May 1976 the NCB announced a £1million scheme to improve the coal winding facilities at Bold colliery. The scheme, which involved the installation of skip winding in the No.1 Shaft, was completed in the summer of 1977. From then on all the colliery’s output was wound up one shaft, instead of two, and unloaded automatically on the surface.
OUPUT DETALS INCLUDING PRODUCTIVITY AND MANPOWER FOR RECENT YEARS
OUTPUT (tons) |
OUTPUT PER MANSHIFT (cwt) |
MANPOWER | |
---|---|---|---|
1970/71 | 738,157 | 42.5 | 1,579 |
1971/71 | 487,366 | 33.7 | 1,568 |
1972/73 | 719,521 | 44.0 | 1,516 |
1973/74 | 562,860 | 42.6 | 1,450 |
1974/75 | 708,815 | 48.9 | 1,423 |
1975/76 | 633,847 | 43.5 | 1,463 |
1976/77 | 692,464 | 47.7 | 1,470 |
1977/78 | 598,081 | 41.4 | 1,472 |
1978/79 | 735,963 tonnes | 2.41 tonnes | 1,493 |
1979/80 | 709,133 tonnes | 2.32 tonnes | 1,496 |
The changing market conditions led to work being concentrated on three faces working eight machine shifts from January 1982. These faces were T.40’s, working on the dip in unproven ground in the south area, T.19’s, in proven ground, but of limited life and to be replaced with T.29’s and Rushy Park 4’s. The proven T.22’s was to provide spare capacity. In the event, roof conditions on T.40’s deteriorated and the face was stopped after four months to be replaced by T.22’s. T.29’s, an advancing face development to replace T.19’s, had encountered faulting. Its gateroads would be extended and the viable coal worked by retreat. T.19’s had produced well, but with the loss of T.29’s and its replacement, the Lower Florida face, L.1’s, could not be developed in time to replace it. (L.1’s got away in September, 1982). The Rushy Park face, far from running the 2-3 years expected, had encountered faulting and had been stopped in November, 1982, leaving Bold with two faces, L.1’s. which was giving good results, and T.22’s, where performance had not reached its expected levels., T.26’s would be ready for production by March, 1983.
Output had fallen from 720,000 tonnes in 1974-5, with a marginal profit, to 471,000 tonnes in 1981-2 with an £11m loss. The projected loss for 1982-3 was £7m. Faced with the failure of the 1982 plan, it was decided concentrate on retreat mining with the intention of producing around 550,000 t.p.a. with a labour force reduced to 1,080 by March 1984.
To do this, men from the abandoned Rushy Park area would be used to develop L.2’s and L.3’s in the Lower Florida. T.26’s would be worked as an advancing face, to be succeeded by T.27’s and T.28’s as retreat faces. A cross-measures drift from No.2 tunnel would improve access to this area which would, like the Lower Florida, provide about three year’s output. T.29’s would be replaced by further retreat Trencherbone faces.
Longer term output would be provided in the upper seams in the south area, the Crombuke, Lower Florida and the Ince Six Feet. The conveying systems would be uprated and the materials and manriding systems improved. No.2 shaft would be filled and the headgear eliminated.
The losses continued and in March 1984 the Miners’ Strike began. Some regular work, like the recapping of winding ropes was done before the strike. Members of the management team were supervising machinery, like the fans, pumps etc which had to keep running, they were also doing underground inspections. NUM safety men had been withdrawn by June, when management were reporting poor conditions on faces caused by floor lift. This had trapped gearhead motors etc. against the roof and would need dinting to lower them. Chock were becoming ‘fast’ as their rams were fully closed by the pressure. They too would need to be freed before faces could resume work.
The strike ended on March 3rd 1985, but the NCB closed Bold in November 1985.
Further information:
- NMRS Records, Gazetteer of British Collieries.
- National Archive: BT31/34141/9529 (1875) Collins Green Colliery Co. Ltd
- National Archive: BT31/15084/31838 (1890) Sutton Heath & Lea Green Collieries Co. Ltd
- National Archive: BT31/38359/166666 (1920) Sutton Heath & Lea Green Collieries Ltd
- St Helens Collieries, Accidents & Incidents (May 2015)
- Colliery Guardian, 23/12/1892
- Bold Colliery, Stage 11 Proposals for Development of the Wigan Four Feet and Trencherbone Seams and Associated Transport. NCB Memorandum, 21st September, 1971.
- NCB Booklet 1974.
- Colliery Review: 18th January, 1983. Ref BS/JPB/6 (C2) MP2001M
- Sutton Beauty & Hertiage website