THE SNIBSTON COLLIERIES
The Snibston Collieries were commenced in 1831 by George and Robert Stephenson. The Stephensons were engaged in the building of the Leicester & Swannington Railway and had taken up residence at Alton Grange situated on the south side of the Long Lane (Coalville) to Ashby de la Zouch road. With collieries already established on the concealed part of the Leicestershire coalfield (the Eastern Basin) close to the route of the Leicester & Swannington Railway, the two Stephensons deduced that there was a good possibility of establishing a successful colliery in the Long Lane (Coalville) area.
SNIBSTON No.1 COLLIERY (SK 425145)
The site chosen for the colliery was north of the Long Lane (Coalville) to Ashby road and close to the route of the Leicester & Swannington Railway. Sinking proved to be difficult. At the top of the shafts 157 feet of Triassic rocks were cut through and these yielded considerable amounts of water. Cast-iron tubbing was inserted in the shaft to hold back the flow of water. Below the Triassic and resting on the Coal Measures, 22 feet of igneous greenstone was encountered. In order to get through this extremely hard rock the Stephensons imported a number of experienced sinkers from County Durham. The Main Seam was intersected at 220 yards and the shaft was continued to reach the Roaster Seam at 284yds. 1ft. 5ins. to the floor of the, seam. Beyond the Roaster coal the shaft was continued for a further 14 yards to form a sump. Several other coal seams were intersected by the shaft but only the Main and the Roaster Seams were worked at Snibston No.1 Colliery.
In working seams north of the colliery towards Swannington, the area where the coal measures were exposed was reached. This area had been intensively worked for centuries, with old workings uncharted, and was heavily water-logged. An unworked barrier of coal had ostensibly been left in the Main Coal Seam as a protection for workings down dip to the south. When the pumping engine at Calcutta Colliery failed in 1882, rising water in the old workings over-topped the barrier and flooded Snibston workings. A court case ensued in which allegations and counter-allegations were made that the coal barrier had been reduced (or perhaps breached) by illegal extraction. Snibston No.1 Colliery closed in the 1880’s and never re-opened.
SNIBSTON No.2 COLLIERY (SK 418145)
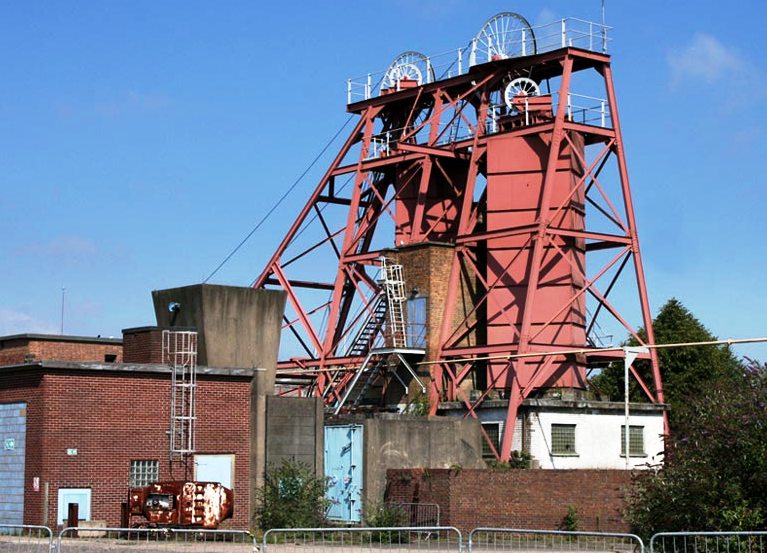
Snibston No 2 Colliery 1983
Copyright © Healey Hero and licensed for reuse under this Creative Commons Licence
The colliery was commenced in 1832. Two shafts were sunk, 9 yards apart. The downcast shaft was 8 feet diameter and the upcast 10 feet diameter. At the top of the shafts 52 yards of Triassic was passed through, this formation lying unconformably on top of the Coal Measures. Unlike Snibston No.1 Colliery, no igneous rock was encountered. Total depth sunk was 309 yards and boring was continued for a further 46 yards and 2 feet. The shafts were lined with 9 inch red brickwork for the first 14 yards, cast-iron tubbing for 90 yards followed by 9 inch red brickwork for the remaining 205 yards to the bottom of the shafts at 309 yards.
Water feeders into the shafts from the Triassic were quite low and during sinking were adequately dealt with by winding the water in barrels.
Although the two Stephensons, father and son, were very closely involved with Snibston No.2 Colliery, the extensive research by Dr. Colin Owen had indicated a strong possibility that the colliery was commenced by a landowner named Fosbrooke of Ravenstone Hall and Snibston Grange. Fosbrooke died in 1830 and Dr. Owen’s research has revealed that his estate, which was advertised for sale in 1831, contained a partially completed colliery. The colliery was described as having an 80 horse power Boulton & Watt engine, three boilers, a whimsey and a range of colliery equipment. A figure of 80 horse power for the engine seems high for the time and could be an error on the part of the selling agent.
To finance the purchase of the Snibston Grange estate, George Stephenson entered into partnership with two Liverpool merchants to form the Snibston Colliery Company, and the purchase was made in 1832. Whilst this date is generally regarded as the commencement of Snibston No.2 Colliery, the Stephensons may well have had a flying start by utilising an already partially completed colliery.
Snibston No.2 Colliery was located about half a mile to the west of Snibston No.1 Colliery and was the longest lived of all three of the Snibston collieries. Although there were some hiccups in the 1870’s and 1880’s, the colliery was in use until 1983. The problems arising in the 1880’s were largely to do with drainage due to the waterlogged old workings in the exposed part of the coalfield in the Swannington area.
A description of the Snibston collieries appeared in an 1892 issue of the Colliery Guardian. By this time the collieries were in the ownership of the South Leicestershire Colliery Co. Ltd. Although the writer of the article was very circumspect it may be inferred that the collieries were old fashioned, even by the standards of the time. At this time Snibston No.2 Colliery was the only one in production, No.1 Colliery already being closed whilst No.3 was in the process of being re-opened.
Winding – A tandem headgear was erected over the two shafts, arranged to wind one cage in each shaft. The cages had two decks, each deck carrying two tubs. At the downcast shaft, the tubs were of 5 cwt. capacity, these being used in the north side of the mine where the coal seam was thin. The upcast shaft served the south side of the mine where the coal seam was thicker and the tubs here were of 10 cwt. capacity.
Winding ropes were of plough steel and were 4¾ inches circumference. The cage conductors were of pitch pine, 6in. by 4in. section, two being provided for each cage. The headgear and associated framing were of pitch pine. In 1892 an average of 480 tons of coal were being wound in the course of an 8½ hour shift.
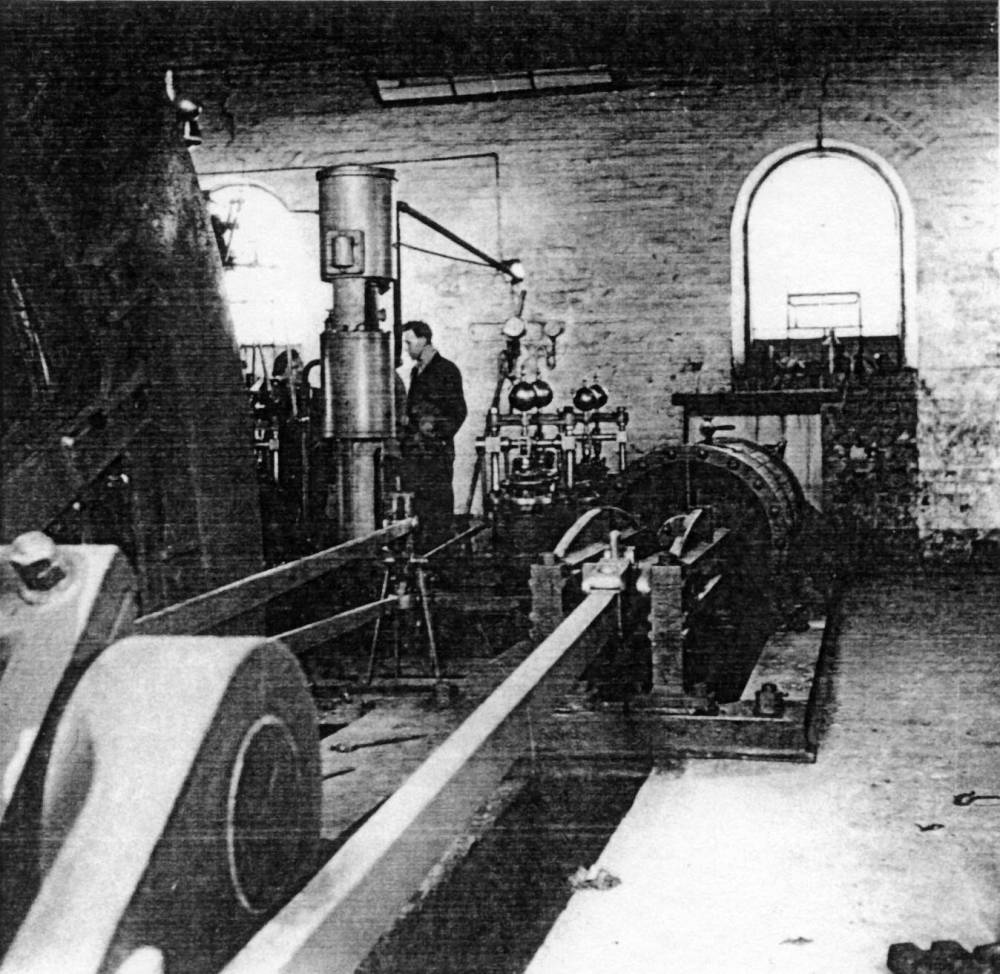
Twin cylinder horizontal winding engine, 30in x 60in
Built by Robert Stephenson & Co c.1852 – Copyright © Raymond King 1959
The winding engine was a twin cylinder horizontal built by Robert Stephenson & Co., Newcastle-upon-Tyne. Anecdotal evidence is that the engine was built in about 1852. Cylinders were 30in. x 60in. fitted with Cornish valves for steam admission and exhaust. The valve chests were arranged in-line at each end of the cylinders, the steam being admitted and exhausted through the same port in the cylinder. The valves were operated, not perhaps as one would expect by Stephenson link motion but by Gooch link motion. To assist in closing the valves ball shaped weights were fitted to the tops of the valve spindles. There was no provision for expansive working and steam was taken for most of the piston stroke. Four-bar slides guided the crossheads and the connecting rods were rectangular section. The cast-iron bedplates were extremely light, a sure sign of antiquity. A 14 feet diameter parallel winding drum was mounted on the crankshaft and on the right-hand side of the drum, adjacent to the right-hand bearing pedestal was an 18 feet diameter flywheel which also served as a brake path. Originally, a foot operated mechanical system applied a strap brake to the underside of the flywheel. Later, the engine was fitted with straight post “clasp” brakes operated by a Whitmore brake engine. It is almost certain that at the same time that this braking system was fitted, the Whitmore overwind/overspeed controller was also applied to the engine.
Messrs. Fraser & Chalmers of Erith, Kent, held the patent rights to the Whitmore control and brake system but many of these units were made under licence by Messrs. H.J.H King of Nailsworth, Gloucestershire.
This winding engine was in service until 1959, when it was replaced by an electric winding engine in a new engine house. The shafts had ceased to be the main coal winding shafts around 1914. Fortunately, a photographic record was made by the late Mr. Raymond King of the steam winding engine shortly before it was taken out of service.
A third shaft was sunk at Snibston No.2 Colliery in 1914. This was of conventional layout with two cages being wound in the shaft. The winding engine was a twin cylinder horizontal made by Robey & Co. Ltd., Lincoln. Drop valves for steam admission and exhaust were fitted to the cylinders. Governor controlled cut-off gear was provided to obtain expansive working.
In the East Midlands, the National Coal Board initiated a policy of replacing winding shafts by cross-measure drifts where this was a feasible proposition. With trunk conveyor belts installed, the drifts became the main coal hauling facility. At Snibston No.2 Colliery a drift was put down from the surface in 1963. The shafts were retained for ventilation, winding men and materials and emergencies. Winding had already been electrified at the two old shafts and the steam winding engine at the 1914 shaft was also subsequently replaced by an electric winding engine. The headgears remained a prominent feature of the colliery with the timber tandem headgear at the two old shafts being replaced by a steel structure. The original steel RSJ headgear at the 1914 shaft was retained in service.
Boilers – In 1892, steam was being supplied by seven egg-ended boilers, 5 feet diameter plus one Cornish boiler, all working at 55 pounds per square inch steam pressure. The boiler tops were insulated with “composition” and were roofed over, this latter feature being quite a luxury at a colliery. Boiler feed was by two live steam injectors made by Sharp, Stewart & Co. One injector was normally in use with the other in reserve. The main source of feed water was a well 28 yards deep from which the water was lifted and delivered to an overhead tank to supply the injectors. The well pump was driven by a single cylinder steam engine, 12in. x 20in., geared 1 to 3 to the well pump shaft. At the time of the Colliery Guardian report it was intended to sink the well to 50 yards depth in order to tap into the Triassic formation.
A secondary source of boiler feed water was surface water and collected rain water which was pumped into another high level tank supplying the injectors by a steam driven pump.
Subsequently the above described boilers were replaced by a range of Lancashire boilers working at a higher steam pressure. These would be necessary to supply the 1914 Robey winding engine. It is possible (or probable) that the old Stephenson winding engine was supplied with steam at a lower pressure through a pressure reducing valve. These boilers in turn were rendered largely redundant in the modernisation schemes carried out by the National Coal Board. Two boilers survived in the 1970’s serving the much reduced steam demand of the colliery.
Pumping – The make of water into the mine was minimal, most of it being seepage into the shafts. This water was raised by the winding engine in two hours during the night according to the Colliery Guardian report.
Ventilation – In 1892, ventilation was provided by two furnaces. These caused air circulations of 46,000 cubic feet per minute in the workings to the north and south of the colliery. A shallow shaft was sunk (c.1892) from the surface surmounted by a chimney and connected by a horizontal tunnel to the upcast shaft. This was to improve the mine air flow up the upcast shaft by eliminating the throttling effect when the cage was at bank.
Underground Working – According to the 1892 Colliery Guardian report, the workings were entirely in the Roaster Seam to the north and south of the shafts. These workings were served by North and South levels respectively each about a mile in length. North of the shafts the seam yielded on average 2ft. 9in. of coal and small tubs of 5cwt. capacity were in use in this section of the mine.
In the shafts a seam of coal was present above the Roaster, with about 4 yards of intervening strata between them. To the south this intervening strata thinned until the two coals joined to form a single seam 5ft. 8in. thick. Large tubs of 10cwt. capacity were used in this section of the mine.
All workings, North and South were on the longwall face system. Naked lights were used throughout the workings, although a safety lamp was kept burning at each working place as a precautionary measure.
Underground Haulage – Apart from a 600 yard self-acting incline in the North workings, all haulage was by pony and horses, about 50 being employed. At this time (1892) the installation of engine powered endless rope haul ages on the main levels was being considered.
Coal Preparation – In the late nineteenth century, coal preparation for the market at the colliery was rudimentary. Large coal was picked straight off the tubs by hand and deposited in railway wagons. The tubs and what coal remained in them, were then raised oh a creeper incline and tipped on to fixed bar screens for grading into cobbles and nuts, the “slack” falling through the screen. House and steam coal were sorted separately. The creeper was driven by a steam engine having a 9in. x 12in. cylinder.
Seams Worked (1952) | Middle and Nether Lount, Yard, Thin and Thick Roaster |
Manpower (1952) | 615 Underground, 207 Surface |
CLOSURE | 1983 |
SNIBSTON No.2 COLLIERY – Summary of Shaft Section
Seam | Depth from Surface | ||
Yards | Feet | Inches | |
Seam of coal | 69 | 2 | 7 |
Seam of Coal | 78 | 0 | 11 |
Seam of Coal | 93 | 0 | 0 |
Seam of Coal | 104 | 1 | 1 |
Slate Seam | 112 | 1 | 1 |
Seam of Coal | 123 | 0 | 2 |
Seam of Cannel | 142 | 0 | 7 |
Seam of Coal | 157 | 0 | 6 |
Main Coal Seam | 177 | 2 | 4 |
The Smoile Seam | 187 | 2 | 0 |
Upper Lount Seam | 197 | 0 | 1 |
Middle Lount Seam | 213 | 1 | 6 |
Nether Lount Seam | 216 | 2 | 6 |
Seam of Coal | 225 | 1 | 11 |
Seam of Coal | 237 | 2 | 2 |
The Roaster Seam | 243 | 0 | 4 |
Seam of Coal | 264 | 0 | 8 |
Seam of Coal | 289 | 2 | 10 |
Total depth sunk | 309 | 0 | 0 |
Boring | |||
Coal | 347 | 1 | 2 |
Total sunk and bored | 355 | 1 | 2 |
SNIBSTON No.3 COLLIERY (SK 420154)
The date of commencement of this colliery is rather obscure. It was located close to the former Leicester & Swannington Railway near the top of the Swannington Incline, to which line a siding connection was made in about 1850. As the Swannington line had opened in 1833, the date of the siding connection may indicate the start of operations at the colliery.
Two shafts were sunk, 8 yards apart, the downcast shaft being 8 feet diameter and the upcast, 7 feet diameter. Total depth sunk was 263 yards, 1 foot and 9 inches. The Main Coal seam was intersected at 184 yards, 2 feet and 8 inches, and the Roaster Seam at 260 yards, and 9 ins. By the mid-1880’s or thereabouts the available Main Coal and Roaster seams had become exhausted. The colliery was closed and the shafts were filled in.
In the early 1890’s work started to re-open the colliery and by 1892 the two old shafts had been re-excavated down to the Middle Lount Seam. The depth re-sunk was 224 yards to the Middle Lount plus an additional 16 yards to form a sump, making a total re-sinking of 240 yards. When the shafts were originally sunk the lining consisted of 14 yards of 9 inch red brick followed by 90 yards of cast-iron tubbing. Below the tubbing, the lining reverted to 9 inch red brick. In the re-sinking the original cast-iron tubbing was retained but the brickwork below this was mostly renewed.
Winding & Boiler Plant – A new winding engine was obtained for the re-working of the colliery. This was built by Messrs. J.D. Leigh of Ellesmere Foundry, Patricroft, near Manchester. It was a twin cylinder horizontal engine with cylinders 30in. x 60in. and fitted with Cornish valves for steam admission and exhaust. The winding drum was of cast-iron construction and was fitted with a foot operated mechanical brake. One cage was wound in each of the two shafts.
Five Lancashire boilers were installed, with the benefit of being roofed over. Working pressure was 40 pounds per square inch although the boilers were constructed for 60psi. These were low pressures even for the time and it seems likely that the boilers were second-hand to the colliery. Boiler feed was by two live-steam injectors, one in operation and one in reserve.
Underground Workings – The Middle Lount Seam yielded 1 foot thickness of good house coal and approximately 4 feet thickness of steam coal.
Coal Preparation – Preparation of the coal for the markets was entirely by hand sorting into large cobbles and “nuts” for both types of coal.
CLOSURE – The re-working of the colliery was obviously not a success and the colliery closed for the final time about 1895.
SNIBSTON No.3 COLLIERY- Summary of Shaft Section
Seam | Depth from Surface | ||
Yards | Feet | Inches | |
Triassic Measures | 40 | 2 | 0 |
Seam of Coal | 45 | 2 | 0 |
Seam of Coal | 55 | 0 | 7 |
Seam of Coal | 58 | 0 | 7 |
Seam of Coa | 62 | 1 | 11 |
Seam of Coal | 69 | 2 | 11 |
Seam of Coal | 83 | 2 | 0 |
Seam of Coal | 91 | 1 | 11 |
Seam of Coal | 106 | 2 | 0 |
Seam of Coal | 118 | 2 | 8 |
The Slate Seam | 126 | 1 | 7 |
Seam of Coal | 144 | 1 | 1 |
The Cannel Seam | 154 | 0 | 8 |
Seam of Coal | 166 | 1 | 8 |
Seam of Coal | 170 | 2 | 8 |
The Main Coal Seam | 184 | 2 | 8 |
The Smoile Seam | 193 | 1 | 10 |
Upper Lount Seam | 204 | 0 | 9 |
Middle Lount Seam | 224 | 0 | 9 |
Nether Lount Seam | 229 | 1 | 7 |
Seam of Coal | 237 | 1 | 10 |
The Roaster Seam | 260 | 0 | 9 |
Depth Sunk | 263 | 1 | 9 |
Copyright © NMRS Records: Geoff Hayes Collection

OS Map, Leicestershire XXIII.NE 1881
Reproduced by permission of the National Library of Scotland