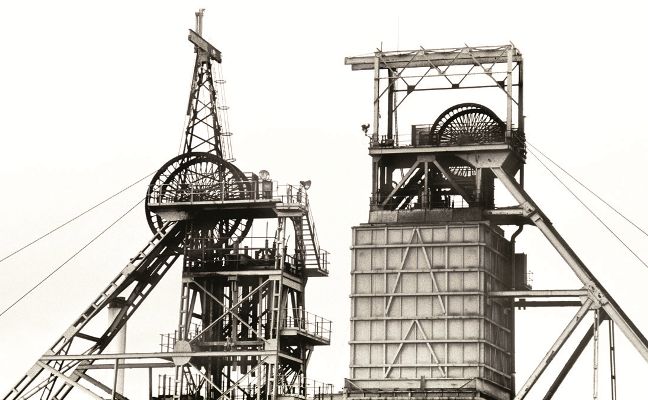
Bickershaw Colliery Headgear 1989
Copyright © Frazerweb and used with permission
In 1830 the first shaft was sunk by Turner and Ackers, but not much is known of these workings.
In 1872 work started on two new shafts, No 1 (489 yards deep) and No 2 (492 yards) to work the Crombouke & Pemberton Five Feet seams and the White & Black mines. In 1877 shafts No 3 & No 4 (both 690 yards), were sunk to the King Coal mine. Another pit, No.5 was completed before the outbreak of war in 1914.
In 1933, No 3 & No 4 shafts were deepened to 779 yards and 787 yards respectively to open up the Peacock and Plodder mines. The closure of Abram Colliery resulted in its workings being merged with Bickershaw.
Nationalisation brought about a re-organisation of the pits in the area. No.5 shaft was abandoned in 1950, and a year later two horizontal 16 feet wide by 13 feet high tunnels were driven 2,750 yards in a southerly direction from No 3 & No 4 shafts to the Crombouke seam. Two similar tunnels were driven 1,500 yards west to the White and Black seams.
- On the 10th October 1932 nineteen men drowned due to an overwind, which caused the cage they were travelling in to enter the shaft sump which was full of water. The full report can be found here.
- On the 7th January 1942 six men we killed and 4 others injured in an explosion, thought to have been caused by a blowout of gas through the stopping from old workings. The explosion appears to have been relatively small and was not heard in other parts of the colliery, but some men began to suffer from the effects of afterdamp. The full report can be found here.
- On the 10th October 1959 five men died from Carbon Monoxide that leaked out from an explosion in an abandoned district. The full report can be found here.
In 1973 works started on transforming the colliery into a “NCB Super Pit”, completed in 1976, it linked Bickershaw underground with the neighbouring Parsonage and Golborne collieries. This required the installation of 7 miles of conveyor belt underground to bring the coal extraction to the surface at Bickershaw. Parsonage colliery continued to be used for winding men and materials until 1983.
Of the coal produced, 90% went to power stations for generating electricity, the remaining 10% went to the industrial and domestic markets.
After the closure of Golborne Colliery in 1989, the pits production target was set at an increased 20,000 tonnes a week. However, with targets consistently missed, British Coal submitted a report showing the colliery to be unprofitable. As a result of this, both Bickershaw and Parsonage Collieries finally closed in 1992.
Further information:
The following is Copyright © NMRS Records: G. Hayes Collection
COLLIERY | BICKERSHAW (PLANK LANE) | ||||||
---|---|---|---|---|---|---|---|
LOCATION | Plank Lane, N. of Leigh Arm of Leeds & Liverpool Canal | ||||||
OWNERS |
|
Shafts
No.1 Pit – commenced 1872, completed 1877 to 489 yards.
No.2 Pit – as above
No.3 Pit – commenced 1877 and sunk to 650 yards, deepened to 779 yards 1933 – 1938
No.4 Pit – final depth 779 yards.
No.5 Pit – commenced 1907, sunk to 305 yards to Ince Yard Mine.
Deepened to Crombouke Mine (Ince Four Feet) at 334 yards, 1921.
Winding
No.1 Pit – Twin cylinder horizontal winding engine, maker not known. Rebuilt by John Wood & Sons, Wigan, 1960. As rebuilt cylinders 36 inches x 72 inches, piston valves with independent drop cut-off valves, Gooch link motion, parallel drum 17 feet 3 inches diameter, post brakes, Melling controller. Headgear originally wood, replaced 1930s by lattice girder headgear removed from closed Abram Colliery. Engine replaced by electric winder 1977.
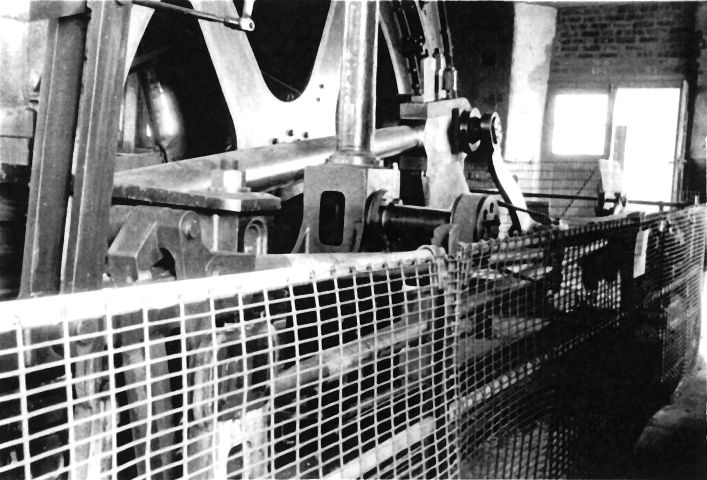
Bickershaw No.1 Pit – Winding engine as rebuilt with piston valves and independent drop cut-off valves
Copyright © NMRS Records: G. Hayes Collection
No.2 Pit – Originally steam winding engine and wooden headgear. Latterly electric winder and RSJ headgear.
No.3 Pit – Twin cylinder horizontal winding engine, Walker Bros. 1881, No.4342. Cylinders 36 inches x 84 inches, slide valves, parallel winding drum. Rebuilt by Walker Bros., 1936/37. New cylinders 32 inches x 84 inches, Cornish valves with governor controlled trip gear, Gooch link motion, horizontal reversing engine. Fast and loose winding drums each 18 feet x 4 feet with post brakes, multi-toothed clutch (hand operated) VISOR overwind/overspeed controller and gear drive for two VISOR controllers. Later fitted with Melling’s pneumatic controller and two Melling’s brake engines. RSJ headgear, originally wooden headgear. Engine replaced by electric winder 1977.
![]() |
![]() |
|
Bickershaw No.3 Pit – Winding engine as rebuilt with 32 inch x 84 inch cylinders, Cornish valves and trip gear |
No.4 Pit – Completely re-equipped latter 1930’s. Electric winding engine with skips, the first installation in the UK. Automatic electric winding engine by Metropolitan – Vickers. mechanical parts sub-contracted to Walker Bros., Works No. 37470, 16-4-36). Specification called for two – 1750hp. motors running at 350rpm with Ward-Leonard control system. Winding from 779 yards. Headgear RSJ construction.
No.5 Pit – Twin cylinder horizontal winding engine by John Wood & Sons Ltd., Barley Brook Foundry, Wigan, 1908, Nos.1581 & 2. Cylinders 30 inches x 72 inches, piston valves, parallel winding drum. Engine removed 1952, overhauled by makers and installed as temporary winder for re-furbishment and development of Agecroft No.3 Pit. Headgear at No.5 Pit of timber construction which survived until closure of shaft.
Compressed Air
Cross-compound two-stage horizontal air compressor supplied 1907 by Walker Bros. (No.13290). Steam cylinders 26 inches + 46 inches by 54 inches stroke, air cylinders 26 inches + 42 inches x 54 inches Corliss valves, Dobson valve gear, steam 100psi., air 75/80psi. 16 ton flywheel. Similar compressor supplied 1915.
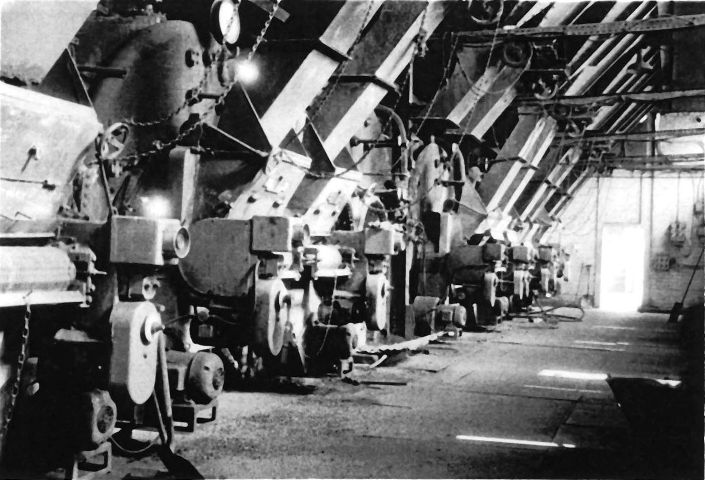
Bickershaw – Cross-compound 2-stage air compressor by Walker Bros., 1916
Copyright © NMRS Records: G. Hayes Collection
Ventilation
Double inlet Guibal (or “Leeds”) fan 46 feet x 12ft., supplied 1882, powered by duplicate tandem compound engine.
Second identical fan appears to have been installed subsequently.
Walker MULTI VANE fan supplied 1932/33 No.34674, 5 feet diameter x 2 feet 6 inches wide, single inlet, complete with pulleys, steel casing and chimney, electric motor and double leather belt drive.
Walker “Indestructible” fan supplied 1933 (No.34934), 20ft.diameter by 7 feet 6 inches wide, rope pulley 9 feet diameter with 12 – 1¾ inch hemp ropes. Cross-compound engine (No.34938) 22 inches + 33 inches x 36 inches, Corliss valves, Dobson valve gear, 110rpm.
Hick, Hargreaves HIVAC ejector condenser and rotary extraction pump.
Boilers (as seen 1975)
Eight Lancashire boilers approx. 8 feet x 30 feet, made by Spurr, Inman of Wakefield, 105 Psi., six boilers fitted with chain grate stokers, two boilers methane fired. Horizontal tube economiser, Weir boiler feed pumps.
Round section chimney with “B.C. LTD. 1937”, induced draught fan at base.
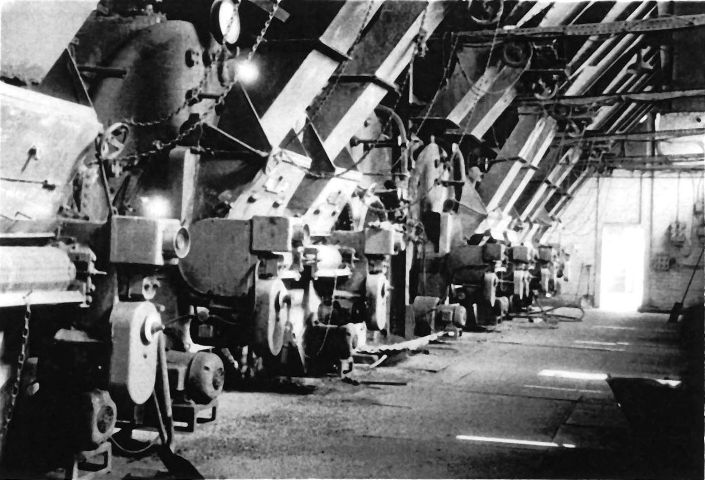
Bickershaw – Lancashire boilers by Spurr, Inman of Wakefield fitted with chain grate stokers
Copyright © NMRS Records: G. Hayes Collection
Power (1931)
Electricity (2200 volts), compressed air, steam.
Seams Worked (1931)
Bickershaw Seven Feet, Crombouke, Pemberton Five Feet, Trencherbone, Wigan Four Feet, Top Yard, Bottom Yard.
Personnel – U/G 1549, S/F 338
Seams Worked (1954)
Ince Seven Feet, Rams (Ince Furnace), Bottom Four Feet, Wigan Six Feet, Bickershaw Six Feet, Haigh Yard, Wigan Two Feet.
Workforce – U/G 2022, S/F 560
Peak production (1951) – 875,000 tons.
Underground Developments
Golborne and Parsonage collieries linked to Bickershaw 1975. Bickershaw became central coal winding colliery.
CLOSURES
No.5 Pit, abandoned and filled in 1952
No.2 Pit abandoned and filled in 1978
Complete closure 1992
NOTES
A catastrophic overwind took place at No.3 Pit on 10 October 1932. The detaching hook on the ascending rope released the winding rope and capel which went over the headgear pulleys and crashed into the engine house causing extensive damage. The cage was held in the headgear by the detaching hook and detaching bell.
The descending cage smashed through the timbers at the bottom of the shaft and plunged into the water-filled sump. Nineteen of the twenty miners riding in the cage were drowned. The sole survivor died some months later.
Copyright © NMRS Records: G. Hayes Collection
Return to previous page