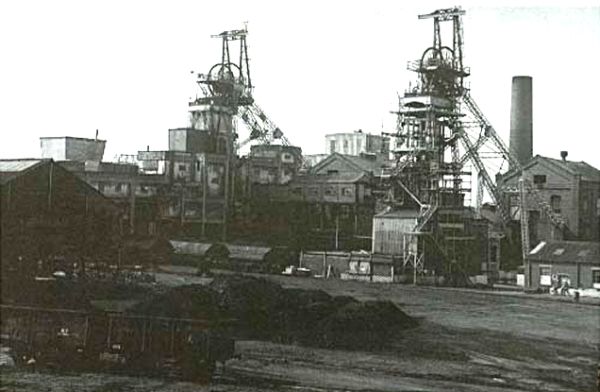
Ravenhead Colliery
Source Wikipedia
There were at least three Ravenhead collieries along the course of Burtonhead Road in the 19th century. The older, and most northerly, was a neighbour of Gerrards Bridge Colliery, which had been abandoned in the late autumn of 1864. In May 1865 the Mines Inspector wrote to the owners of Croppers Hill and Ravenhead collieries advising them of the threat of inundation, especially to the latter, posed by the water collecting in the Gerrards Bridge workings. The two earliest collieries were abandoned at this time, therefore, and Bromilow, Haddock & Co. sank a new one, to a depth of 494 metres, between 1866 and 1867. In 1876 the companies owning Ravenhead, St Helens and some smaller pits in the area merged to form the St Helens Collieries Co. Ltd. What had been St Helens Colliery, near the glass works, became Crop and Deep Pits. These closed in the mid-1920s. St Helens, Alexandra colliery also continued until the mid-1920s, when it became a pumping pit for Ravenhead. Sherdley colliery closed in 1940 and it too became a pumping and fan pit for Ravenhead.
Ravenhead’s two shafts (Nos.10 & 11) were both brick lined to 4.6 metres diameter, and used for the winding of coal, men and materials. No.10 Shaft, the upcast, was 497 metres deep, but wound from an inset at 483 metres. It had flexible rope guides and two, two-deck cages, with each deck capable of holding two 10cwt capacity tubs, or two tons per wind, and a shaft capacity of 75 tons per hour. By 1968 the upcast shaft was only used for manriding.
No.11 shaft, the downcast, had a total depth of 307 metres, but was wound from a depth of 300 metres. Fitted with flexible rope guides, the two three-deck cages, with each deck taking two 10cwt tubs per deck, or three tons per wind, and a shaft capacity of 110 tons per hour. The tubs were pushed into the cages by pneumatic rams, both on the surface and underground. The winding engines at both shafts were electrically driven.
Methane drainage was used in the No.11 Pit for several years. From March, 1958 a Davidson radial flow fan provided 256,000 cubic feet per minute at a water gauge of 12.9 inches. A booster fan was installed in the No.11 Pit to ventilate its extended workings. Near the end of the colliery’s life, production was concentrated on one retreat face, in the Wigan Four Feet seam, so adequate ventilation was given by the surface standby fan, which provided 135,000 c.f.m. at 6 inch water gauge.
Over the years, the following seams were worked:
1905-1930, 1940-1950 | Ravenhead Higher Delf |
1905-1938, 1947-1950 | Main Delf |
1905-1940 | Bastian |
1910-1920 | Yard |
1915-1920 | Four Feet |
1925-1935 | Flaggy Delf |
1925-1961 | Rushy Park |
1925-1940 | Little Delf |
1930-1940 | Pigeon House |
1935-1940 | Park |
1950 | Doe |
1947-1965 | Flaggy Delf |
1947-1950 | Little Delf |
1952-1955 | Wigan Five Feet |
1952-1955 | Wigan Four Feet |
1952-1967 | Arley |
1955-1961 | Trencherbone |
1955, 1967-1968 | Wigan Four Feet |
1960-1965 | Peacock |
The Wigan Four Feet seam at Ravenhead was 2.4 metres thick, but only 1.9 metres of it were taken. The rest was left to create a good floor in order to stop the props sinking into a layer of soft fireclay under the seam. The roof was mainly sandstone.
The district was developed by driving gate roads, lined with 14 ft x 10 ft arches with steel lagging, in the Wigan Four and Five Feet seams using shotfiring, then mucking out with gathering arm loaders onto belt conveyors via stage loaders. Advances averaged 27.5 metres in each roadway per week, and the face began producing coal in March 1966. Problems were encountered when crossing old pillars in the Peacock Mine workings 26.5 metres below, but these were overcome by intensive packing across the affected section.
The face was 250 metres long and worked across the seam gradient (1 in 5.6) giving a dip of 1 in 6 from the tail to the main gate. The roadways also dipped inbye at 1 in 20. The face was supported using 2.7 metre long bars, at 1.05 metre centres, with five Dowty hydraulic props per pair of bars. The stable was supported by 4.27 metre long bars and Dowty props. The coal was cut using a 125 h.p. Anderson Boyes Ranging Drum Shearer, with a 48 inch drum and 27 inch web. A 100 h.p., B.J.D. orthodox shearer, with a 60 inch drum and 27 inch web, was used in the stable hole. Coal came off the face on an armoured conveyor, onto a stage loader, and then onto the main belt.
The decision to use retreat mining was strongly influenced by the seam having a history of spontaneous heating. The strata between the Wigan Four Feet and the Peacock Mines had already been drained when the latter was worked. Nevertheless, a dummy return was maintained at the return ends of the face to minimise flushing of the gas from the adjoining waste. This worked and air samples were well within limitations. The dummy return and Main return levels were sealed off at approximately 64 metre intervals and new connections established. In the Main return roadway, however, methane drainage was achieved by putting up 30 metre long holes at 45 degrees and at 14 metre intervals. Extraction rates of 60 cubic feet per minute at 50% purity were normal, but they fell to 15 cubic feet per minute at 50% purity.
Face performance was affected by shaft capacity which restricted output performance per machine shift to 650 tons. Full production was done on two shifts, bit it was restricted to three hours on the third shift to allow for shaft examinations, material winding etc.
Five 36 inch belt conveyors carried coal from the face to the loading point, a distance of 2,300 metres, where it was loaded into 10cwt tubs. An endless-rope haulage then hauled the tubs to the shaft bottom, some 730 metres away. No.11 Pit had two rope-hauled manriding systems, respectively 575 and 880 metres long. Travelling outbye was helped by 1,100 metre ride able conveyor belt.
On the surface, a 120 tons per hour Baum washery, fitted with Acco shale discharge gear, gave a clean four-inch product. Before nationalisation the colliery had seven Lancashire boilers, all from 40 and 50 years old, and a 400Kw generator operated by low pressure steam from the old No.11 pit winder, together with a small supply purchased from MANWEB. By 1952 all the electrical power supply came from MANWEB at 6,600 volts transformed down to 2,200 volts. Two Lancashire boilers were kept to heat water for the pithead baths, offices and workshops.
In the six weeks up to March 30th 1968 the lowest and highest weekly tonnages of saleable coal were 4,759 and 5,668 respectively. By April 1968, however, output had risen to 900 tons per day, at 44 cwt per man shift, with 477 men. This was achieved by reorganising the underground transport system and concentrating on ‘retreat’ working in the Wigan Four Foot Seam.
The colliery had exhausted its workable reserves by October 1968 and ceased production, with most of its 420 men transferring to neighbouring pits. Nevertheless, Ravenhead had earned its place in mining history because it was where James Anderton developed the famous Anderton Shearer Loader.
Further information:
- NMRS Records, Gazetteer of British Collieries.
- National Archives: BT31/38688/10750 (1876) St Helens Collieries Co. Ltd